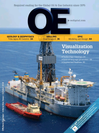
Page 35: of Offshore Engineer Magazine (Oct/Nov 2014)
Read this page in Pdf, Flash or Html5 edition of Oct/Nov 2014 Offshore Engineer Magazine
The GE (Hydril) MaxLift pump aboard equivalent weight fuid – eliminating the
Drilling the drillship. Pacifc Santa Ana additional mud weight.
Photos: Pacifc Drilling.
Statoil also uses a pump and mud to another, drilling has to stop and casing return line, but the pump is attached has to be cemented in to stabilize the hole, to the riser 1100ft below the surface. taking up drilling time and money. Mud flls the riser up to a level set by
Generally, in conventional single- the pump and then circulates up a mud gradient drilling, the deeper the well, the return line to the surface. The rest of the more casing strings have to be set. And riser is flled with air, which does not because each string has to pass through require a handling system. the previous one, the casing – each “We don’t call it dual gradient. It’s zero string of which extends all the way to gradient because there aren’t two fuids,” the surface – shrinks in diameter as the said Uno Holm Rognli, Statoil’s vice Keeping the well deepens. This could mean the well president of drilling and wells for the US can’t reach the target zone at the desired offshore.
diameter, making the production string
Diferent goals too small to produce economically, and ‘window’ open lead to diferent systems the well, in effect, un-drillable.
Dual-gradient or managed-pressure The difference in systems is because drilling offers a way forward. If the mud Statoil and Chevron are coming at the level in the marine riser can be dropped, problem from different starting points. the pressure gradients in the wellbore Chevron wants to maximize the window start at a lower level, in effect widening and reduce the number of casings or inter- the drilling window. mediate liners required.
In the Chevron-Pacifc DGD case, the Statoil’s goal is more modest: to stay within the narrow window that is available by eliminating fuctuations between static and dynamic circulating pressure, an issue in conventional drill- ing. If it saves having to install extra casings or liners, that’s an added beneft. “We want to simplify it,” Rognli said.
Statoil engineers chose 1100ft for the pump depth because they consider that ade- quate for now. “We could put be a stronger business case for change. less effective deeper down, it deeper, but it would mean a
Chevron’s project manager for dual-gradi- he said. “We are nearing their longer umbilical, a longer mud ent drilling implementation, Ken Smith, limits to deliver today’s oil return line. So everything gets outlined the challenge at the 2014 Offshore targets in deepwater,” Smith more expensive,” Rognli said.
Technology Conference (OTC). Starting said. “It’s time to change the Deeper placement of the pump 15 years ago, narrowing windows began game.” is under study, but “we are creating problems for drilling convention- starting carefully,” said Roger
Mud weight versus pore ally, most notably by requiring many more
Stave, senior technology advi- pressure, fracture gradient casing strings, each one narrower than sor to Enhanced Drilling.
The basic problem is that the In both the Chevron and the previous one, resulting in cementing
The drillship at Chevron’s Anchor prospect in Pacifc Santa Ana weight of the drilling fuid in Statoil systems, the drilling troubles, tight down-hole tool tolerances
Gulf of Mexico.
the wellbore must stay within window, in effect, starts closer and narrower-than-desired completions.
“Today, it’s only gotten more chal- limits as the drill bit passes through vary- relevant gradients start at the seafoor. In to the seabed rather than at the surface, lenging. We routinely drill nearly ‘un- ing geologic strata on its way to target Statoil’s ECD-M, gradients while drill- reducing the impact of water depth. It’s drillable’ wells,” he said, citing wells depth. If the mud weight is too heavy, it ing can start as deep as 1100ft below the almost as if the rig were on land. more than 30,000ft in total depth drilled can fracture a formation and cause col- surface, the depth at which Statoil has Statoil employs centrifugal pumps in in waters more than 6000ft deep with lapse of the wellbore as mud fows out chosen to place its pump in coming tests. a series of three, attached to the riser. mechanical risk indexes above an astro- into the neighboring strata, a phenom- In both cases, the mud load is lighter. “We’re using the same pump as those nomical 9000. The newest rigs are now enon called “losses.” If the mud is too The Chevron system flls the wellbore used for riserless mud return (RMR), and capable of drilling to 40,000ft, capability light, it can’t prevent uncontrolled intru- with drilling mud up to the seafoor. they have been around several years, on a that will be needed to reach the industry’s sion of water, oil or gas into the wellbore, There, the MaxLift pump circulates the lot of wells,” said John-Morten Godhavn, growing portfolio of ultra-deepwater proj- a phenomenon called “kicks.” mud back to the surface via a separate a Statoil researcher and managed pres- ects. But the technological advances that If mud weight becomes too heavy or too mud return line. The riser from the sure drilling specialist.
have enabled drilling beyond 30,000ft are light, as the well deepens from one strata seafoor to the rig is flled with seawater Riserless tophole drilling, Ziegler says, oedigital.com October 2014 | OE 37 000_OE1014_D&C1_Bruce.indd 37 9/23/14 1:17 PM