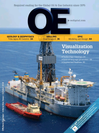
Page 36: of Offshore Engineer Magazine (Oct/Nov 2014)
Read this page in Pdf, Flash or Html5 edition of Oct/Nov 2014 Offshore Engineer Magazine
systems, one for handling drilling mud, another for the seawater-like fuid in the marine riser, and another for the seawater powering the
Drilling pump. The moon pool was redesigned for handling the 450,000lb MaxLift pump in addition to the usual subsea equipment.
The Statoil system – designed for retroftting on existing rigs – uses Enhanced
Drilling’s 29,000lb EC-Drill controlled-mud-level system, modifed riser joints, MPO’s
Delta Seal Riser Module with quick closing annular, a riser gas handler system, and
Coriolis sensors for early kick detection.
Whereas Chevron’s busi- ness case revolved around drilling in ultra-deepwater,
The Enhanced Drilling (AGR) pump on the semisubmersible at Statoil’s Troll Field COSL Innovator
Statoil had two goals – to of Norway. Image: Enhanced Drilling.
drill more effciently in is – in essence – the oldest dual-gradient line. A subsea rotating control device sits ultra-deepwater and to extend the life approach because there is no marine riser. above the SPU, providing a mechanical of felds in shallower Norwegian waters.
But it is unusable for taking a well to total barrier between the wellbore and the Both Statoil goals require overcoming depth. Chevron’s seafoor-based MaxLift riser. It allows temporary over-balancing bottomhole pressure issues, but in the pump is quite different. It is an innova- during system operations, while protect- case of mature felds offshore of Norway, tive positive-displacement powered by ing the wellbore from pulses that could the problem is that years of production seawater. “break the window” downhole. have sharply cut formation pressures and
The Pacifc Santa Ana – purpose- increased mud-loss incidents.
GE MaxLift pump key to Chevron DGD built for DGD – has three separate fuid
Statoil’s Enhanced Drilling
The GE MaxLift pump has six,
Conventional Casing Deepwater Casing system meets two needs 80gal chambers, each divided by a diaphragm. Seawater At the Troll feld last March, pumped from the surface pro- Statoil used an ECD-M retroft- vides hydraulic force to move ted semisubmersible, the COSL the diaphragm back and forth, Innovator, to drill a depleted alternately pulling mud from formation, punching a horizontal the well and pushing it to the well 12,500ft and reducing mud surface. The system can achieve losses 75%. “Troll came up as 1800gal/min. Powering it with a kind of frst use because they seawater minimizes electri- had a special need,” Rognli said.
In conventional drilling, window narrows with water depth above borehole, requiring more casing, delays to install it. cal equipment sitting several “What they are using is this sys- thousand feet underwater. There tem to take down the mud level 0 0
Surface are still electronics involved, in the riser, to drill with lower 2000 2000 as the valves that open and pressure, still using water-based
Sea?oor 4000 4000 close, directing fows of mud muds.” 6000 6000
Well bore and seawater, are electronically Troll is in relatively shallow 8000 8000 controlled. water, at just over 1000ft deep, so “Flat Time” 10000 10000
Installing
Both systems are more than the pump in the ECD-M system
Casing 12000 12000 just pumps and return lines. In could be placed close to the 14000
Pore Pressure 14000 the Chevron-Pacifc system, the seafoor, flling most of the riser 16000
Fracture 16000 pump is placed atop the lower with air. “We pulled the fuid
Gradient 18000
Depth 18000 marine riser package. A solids two-thirds of the way down the 20000 20000 processing unit (SPU) sits atop riser, and we got an effect greater 22000 22000 the pump to ensure that solids than if you’d flled the riser with 8.00 10.00 12.00 14.00 16.00 18.00 8.00 10.00 12.00 14.00 16.00 18.00 are small enough to pump with- seawater to the seafoor,” Stave
Pressure out plugging the mud return said.
Source: Chevron, Design by Bruce Nichols
October 2014 | OE oedigital.com 38 000_OE1014_D&C1_Bruce.indd 38 9/23/14 4:13 PM