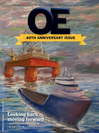
Page 41: of Offshore Engineer Magazine (Jan/Feb 2015)
Read this page in Pdf, Flash or Html5 edition of Jan/Feb 2015 Offshore Engineer Magazine
failure (MTTF) data to support cost- to risk-based assessment and perfor-
Drilling mance-led decision-making for mainte- saving decisions.
Most operators accept that certain well nance scheduling. barrier component failures are inevitable These capabilities are already
A key challenge has and operational constraints may mean enshrined in UK health, safety and been the reticence that they cannot be repaired immediately. environmental practices, and in Norway,
It can be necessary for wells with indi- where the Petroleum Safety Authority of operators to vidual components not in full working stipulates that each well workover order to continue to operate, provided case be assessed per well and based on make data such as risk assessment indicates the risk level reliability data. As regulations evolve, is acceptable. Of course, some types of iQRA’s ultimate aim is to equip operators component reliability operators to make data such as compo- failure call for the well to be shut-in and with the insight to optimize well opera- nent reliability and failure rates avail- repaired immediately, but for the major- tions by identifying potential weaknesses and failure rates able externally. ity of non-critical failures, repairs are in their equipment and pre-empting available externally.
In addition to concerns over data scheduled to take place within a desig- future issues. con? dentiality, efforts to build such a nated timeframe, or when the opportu- database have tended to be limited to nity arises. Ged Lunt is technol- single regions such as the North Sea, or Testing can actually reduce the lifetime ogy manager at Wood focused strongly on speci? c components of the equipment – especially an active replace equipment if another well inter- Group Intetech. Lunt such as the SSSV. Previous systems have component that is opened and shut, each vention is taking place. has been responsible also been badly structured and suffered cycle causing some amount of wear and for delivering the
Meeting user needs from poor quality of data or dif? culty of fatigue. Intetech Well use or access. Given that it is necessary to close The ability to benchmark company Integrity Toolkit valves in order to test the leak rate performance against the global data- (iWIT) software for
Better insight, better decisions across them, using risk-based analysis base is attractive for operators, as is the well integrity management to clients
Wood Group Intetech launched a global to determine that testing can be safely functionality to carry out reliability and including the BG Group worldwide database of well performance data performed less frequently, should extend MTTF evaluations and the provision of operations, Statoil (2000 wells in called iQRA. This online quantita- the lifetime of valves, as well as reducing robust and risk-based evidence to present Norway), Stogit (ENI gas storage com- tive reliability analysis tool provides operating costs. to production managers when requesting pany) and Hess Equitorial Guinea. He operators with access to global well
Access to this kind of reliability infor- that a well be shut-in. has extensive experience in analysis of and oil? eld component performance mation makes it possible for operators to Following the ISO-14224 standard, customer well integrity management information, so operators can identify identify where they have low reliability iQRA also includes failure data analysis, requirements, in interfacing database the highest performing well compo- equipment or potentially a faulty compo- such as critical failures versus degraded systems into the iWIT software and nents, benchmark reliability ? gures, nent, and pre-empt potential failures on failures. These features have been customising iWIT to match company and extract statistical and mean-time-to other wells by taking the opportunity to designed to accelerate the industry shift requirements.
Engineers also need to be able to specify components ? eld development when there is little own-service experience. that fail less frequently in operational conditions that are
It is also possible to compare failure information during the the same or close to those of their assets. They can use a early years to identify whether the failure rate is indicative reliability database subset of information that re? ects their of a higher rate of burn-in failures. These may indicate environmental conditions to select the components by vendor manufacturing or material defects in certain equipment and model. This is particularly useful during an early phase of sources. This is illustrated in Figure 4, which shows a higher failure rate (steeper gradient of the failures failure rate (steeper gradient of the failures curve) in the early life period. curve) in the early life period. •
Fig. 3: Reliability survival function 1.25
Fig. 4: Test failures vs. service life 1.00
Test failures 200 150 0.75 100 50 0.50
Number of failures
Reliability survival function 0 0k2k4k6k 0.25 Service life (years) 0 2.5 5.0 7.5
Trend line failuresFailures
Years oedigital.com oedigital.com January 2015 | OEJanuary 2015 | OE 4343 042_OE0115_D&C3_intetech.indd 43 12/22/14 9:48 PM