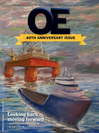
Page 50: of Offshore Engineer Magazine (Jan/Feb 2015)
Read this page in Pdf, Flash or Html5 edition of Jan/Feb 2015 Offshore Engineer Magazine
the top of the single oil-over-water cargo tank, and displaces water removed from the bottom via a central caisson, treated and discharged overboard. Only small
EPIC compensating ballast tanks are required to maintain draft and meet damage stability requirements. At offoad, cargo pumps on the topsides deck transfer the crude via an offoad reel on the weather deck to a shuttle tanker while sea water is pumped into the cargo tank from below.
Risers are routed via a hang off frame located on a cellar deck of the topsides.
All hazardous process equipment is kept in open and freely ventilated space, and provides good, multiple access to emer- gency escape routes, even on this very small facility. Minimal marine facilities A compact-FPSO (C-FPSO) design.
reduce persons on board requirements producing into an attend- signifcantly.
ing shuttle tanker, with the
Conclusion storage capacity as “buffer” whilst the attending tanker It is becoming increasingly important to is off station to unload. As look for means to exploit economically oil production rates drop marginal felds that may be remote, have later in life the smaller Opex short production life, extreme environ- facility is better matched to mental conditions or fow assurance the size of the feld. diffculties. The “closed-loop” oil-over- water approach has helped develop some
A compact-FPSO particularly cost-effective approaches to (C-FPSO) design exploiting stranded and marginal felds, 3
The FPS demonstrated that safely and environmentally. It is clear that
Heave response and wave period charted.
there is room for further in order to continue to drive down Capex, innovation in FPSO design for marginal such as a semisubmersible, or ship- particularly in an era of uncertain oil felds. Can we develop an even lower shaped unit, wave loads typically govern price, much smarter engineering com- cost solution for yet more marginal felds the structural design and often limit the bined with better ways to manage techni- that might be constructed and installed operational fatigue life due to global cal and economic risk is required. for no more than $250 million? loading. For the C-FPSO, the global wave
Ben Smith is a naval
In two studies for North Sea felds with loads are at a minimum and the internal architect within the an estimated life of 7-10 years, Atkins arrangement is set out to focus on load
Oil and Gas business developed a small deep-draft buoy with a carrying horizontal hydrostatic pressure. at Atkins based in single central oil-over-water cargo storage For this reason the structural design of
London. He joined tank combined with a conventional inte- the hull is surprisingly simple. By mak-
Atkins in 2010 grated topsides. This innovative concept ing use of a conventional stiffened plate principally focused on serves as a low Capex – low Opex solu- structure and simple symmetric repeti- the design of assets tion and provides processing and offoad- tive design; the overall construction risk for marginal felds. He graduated with an ing facilities on the smallest platform and engineering timescales from concept
MEng from the University of Southampton. “footprint” affordable. The key features design to unit delivery are minimized. • of this patented concept (GB2507370) are Topsides and operation
Ed Randall is a outlined below. The C-FPSO has been designed to accom-
Hull form modate a conventional integrated topsides • chartered naval
The C-FPSO’s deep draught near sym- payload in the range of 4500 to 6500- architect with a focus metric hull form gives benefcial motions tonne – depending on storage capacity. on early stage design characteristics similar to those of a SPAR. The integrated topsides allows this design where maximum
Heave plates also give the concept inher- to maintain a distinct separation between value can be added. ently high natural periods. The motion the production fuids process systems,
He has project is relatively insensitive to wave direc- power generation and accommodation, managed multi-disci- tion which allows the unit to be spread and the hull systems, including cargo plinary concept, FEED and detail design moored thus removing the need for the storage and offoading. This simplifes projects and leads the foating systems team in London. Randall holds an MSc in turret and swivel found on conventional construction and installation and gives
Naval Architecture from the University of weathervaning FPSOs. fexibility in re-use of the facility.
Southampton.
For a conventional offshore structure During production, the cargo is fed into
January 2015 | OE oedigital.com 52 050_OE0115_EPIC2_Adkins.indd 52 12/22/14 6:49 PM