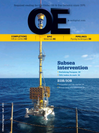
Page 49: of Offshore Engineer Magazine (Apr/May 2015)
Read this page in Pdf, Flash or Html5 edition of Apr/May 2015 Offshore Engineer Magazine
EyebrowProduction might be plagued by several planned (and “You have to pump them in and they go out interventions on at least two wells that unplanned) interventions, says Brian through a service loop in the tree and were shut-in, one of which had been out
Skeels, emerging technology director at they go downhole. You have two produc- of production for 10 years. Stone laid out
FMC Technologies and an adjunct profes- tion bores. You have to pump down one its needs, including the freedom to use DP sor of subsea engineering at the University and reverse out, basically pumping your semisubmersible or DP monohull vessel of Houston.
tool all the way back to the platform rather than a moored MODU.
While Pompano is currently the only when it is done,” he says.
Finding a solution feld using a TFL system in the Gulf of
The key to TFL technology, Skeels
Mexico, it’s not the only one in the world.
says, is understanding how it works and The Pompano feld and its TFL system “What started with Exxon’s SPS project then building and installing the equip- wasn’t a total mystery to Cross Group. at Garden Banks 70/71 back in the 1970’s ment correctly with that “pump down Several team members overseeing the later moved to Shell/Esso’s Central and pump back” understanding in mind. project had previously worked on the
Cormorant project in the UK’s North Sea “If the pipeline is improperly constructed original equipment for BP while at sector in the 1980s, and Statoil’s (Saga (welding slag or misalignment of joints) Saipem, says Larry Klentz, vice presi-
Petroleum) Snorre project offshore Norway or the trees do not feature the right cham- dent, Operations, Cross Group.
in 1992. TFL was also experimented with fers and entry/exit angles, or later on you Cross Group’s proposal provided a new on other North Sea pilot projects for Mobil developed a production problem, the system, which would grant access to each and Conoco in the same era,” Skeels says.
pipe was clogged with paraffns, or you wellbore and annulus through a new
Skeels, who serves on an API had debris issues like sand or corrosion, triple bore selector and valve assembly,
Subcommittee 17 executive committee, you could really get yourself in a bind allowing the work to be done with or says that TFL continues to have its merits. by sticking a TFL tool somewhere in the without a riser. Working with Houston “But, its cachet may have come and maze of piping,” Skeels says. engineering frm OilPatch Technologies gone,” he says, when compared to some of Stuart Morrison, a senior subsea (OPT), the two companies created and today’s lower cost intervention solutions engineer at Stone Energy who over- manufactured this new system that like monohull riserless intervention. saw the completion workover riser would interface with both Cross Group’s
The way the TFL system works is that (CWOR) design and refurbishment for upper intervention package and the exist- tools have to be pumped through a 4.5mi the operator, says another problem is ing triple bore vertical tree/TFL system.
fowline from the Pompano platform few people in the industry with this in- OPT lead the design, analysis, draw- and into a well in order to perform work depth knowledge of TFL systems remain. ings, manufacturing, and assisted with that is typically done with slickline on Additionally, there’s only one company testing of the new system. The work took conventional dry tree wells. This requires that provides the pump-down equipment approximately 18 months, says Gary the TFL tools to be extremely fexible, for TFL systems, Otis (now Halliburton). Galle, associate principal and director of almost like snakes, says Jason Leath,
Director of Projects at Cross Group.
Through-fowline systems
In a 1999 SPE paper by then-BP
Exploration engineers James P. Cordner and John W. Kleinhans, a TFL system, deployed from a moored mobile offshore drilling unit (MODU), was selected for Photo from Stone Energy.
Left: Tree ROV panel. Right: The insert safety valve ROV bucket.
the feld’s subsea template after numer- 2 ous concepts were evaluated . This meant Stone Energy had new markets and new technology, OPT.
The biggest challenge, says Galle, was fg- “Based on the results, the best match- to fnd a way to intervene on its uring out the requirements. Cameron made up of reservoir needs, including uncer- subsea template with an open the original equipment and work on the tainty about both well count and reser- mind, Morrison says, bringing in new system meant working with Cameron, voir management needs, indicated that several intervention companies
Cross Group, Stone Energy, and others to subsea facilities comprised of a 10-well, to offer solutions before eventu- defne and close interfaces.
subsea template structure and designed ally settling on Cross Group.
“We knew we had work to do, for production wells outftted for TFL Galle says by keeping the adaptor’s relative to the template,” Castille servicing would best meet objectives,” design as modular as possible, it allowed says. “The system was in ill-repair they wrote. OPT to evolve with changing needs
TFL was cutting edge technology when and needed to be refurbished. and requirements. “We broke it up into developed almost 30-40 years ago as an Because of the cost of rigs today, enough sub-components so that if we alternate solution to high cost, high mobi- putting a rig on location for a very changed one, it wouldn’t change the lization drilling vessel intervention back minor intervention was not cost overall design,” he says.
into a subsea well. TFL was seen as the effective.”
Stone Energy needed a more The technology economic solution to Pompano’s unique
Deployment of the lower completion package.
Photo from Cross Group.
fexible system in order to carry Cross Group considered several concepts and troublesome reservoir properties that oedigital.com April 2015 | OE 51 050_OE0415_ProdOps_Pompano.indd 51 3/23/15 5:59 PM