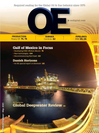
Page 67: of Offshore Engineer Magazine (May/Jun 2015)
Read this page in Pdf, Flash or Html5 edition of May/Jun 2015 Offshore Engineer Magazine
Braced and ready for action – DONG’s
Siri platform, complete with cable stays.
EPIC
Once in place, the tensioning was performed by a jacking system designed by Subsea 7. “Conventionally when ten- sioning stays, you’d use a weight jack,”
Cassie says. “We saw this wasn’t going to work, it would take too long and we felt the risk of thread damage was too high.
We decided to design our own tensioning system, which allowed the cable catenary 150-tonne and the lower clamps to be removed in one stroke; avoiding stand 6.4m from base to nose. possible damage as well as speeding up
Fabricated in two pieces, including the operation.” cast sections (the clamp nose section The system was built into the ends of which supports the cable anchor- the cables. Four hydraulic cylinder rams age), the clamps are then bolted into (500-tonne each with 8/900mm stroke) place using 56 M90 bolts. extended and pulled the cable end pieces
The 60m-long cable stays have a through the bearing plate – all without 355mm outer diameter (including damaging the thread which would hold sheath), and 169 stranded cable, with the cable in place. They were powered each strand comprising seven wires. using a hydraulic power unit designed
However, unlike standard cable to be able to make sure each of the four stays, the stays for Siri had to be cylinders progressed in tandem while the designed to be water tight; this catenary was being pulled out.
added signifcantly to the com- First the stays were each pre-tensioned plexity of the assembly operation. to 500-ton, to take the catenary out of the
A bespoke facility was set up in cable, before being tensioned to 1250-
Dundee, Scotland, to assemble the tonne. In 2012, one clamp was installed, stays, this included a set of articu- followed by a further two in 2013 and lated towers to allow the cable ends the three upper clamps and the cables to be held vertically whilst the end in 2014. The project, carried out over anchorages were sealed with epoxy 350 vessel days using the Seven Falcon, resin and wax to make them water completed in July 2014. tight. Reductions in the platform motion “Once the design was over the were achieved and, as a result, DONG line the next challenge was to install was in a position to remove the restric- it,” Cassie says. tions on manning the 65-man platform
The dive support vessel Seven and return to normal platform operations.
Falcon, with a 250-tonne crane, “We were very pleased with the way meant Subsea 7 had the capability to the procedures worked on the offshore install the clamps. Offshore installa- campaign,” Cassie says. “There was a tion involved complex simultaneous lot of sensitivity around lifting these operations between the dive support large sections of the storage tank. We vessel and platform based operators, had almost no shutdown period on the including rope access technicians. platform, only about 15 days to put in
For the installation of the clamps, pre- the clamps on the north leg because of installed guide clamps were used. Winch access challenges due to the position of platforms, each weighing 150-tonne a the riser.” piece and measuring 15m sq, also had to Refecting on the project, Cassie says
Taking the load – one of the Each lower clamp stands some 6.4m from base be installed at the top of each platform lessons learned were: “Don’t under- top clamps. to “nose”.
leg. The winches, three per winch plat- estimate the challenge of delivering form, the largest with 120-tonne capacity, installed the upper and lower bolts and tolerance of 0.15°,” Cassie says. something innovative and new and would be used to bring the components then an automated bolt rack was used The cables were also installed from the don’t under estimate the ability of good in to place, working with the construc- to locate and tighten the remaining 46 Seven Falcon. Using specially designed engineers to resolve those problems.” tion vessel. A subsea winch was also bolts (each bolt 90mm-diameter, 2m-long installation aids, the operation involved “Are we going to use cables in used to provide supplementary hold back and weighing 300kg), creating a metal to complex simultaneous operations from other parts of the North Sea,” he asks. where needed to control the components. metal grip between the clamp and the leg the vessel and platform based winch “Possibly not, but it is part of our tool kit
Each of the lower clamps, lined with tubular. operators. Key to the operation was to now and refects our general principle a specially selected low yield strength Next, the upper clamps were installed. avoid damage to the cables, particularly around engineering innovative solutions material, was then lowered onto guide “The subsea installation tolerances were the water tight duct and the threaded for mature assets, something we are very clamps in two pieces. Divers/RAT’s very tight. The upper clamps required a upper end of the anchorage. proud of.” oedigital.com May 2015 | OE 69 068_OE0515_EPIC1-Siri.indd 69 4/20/15 3:42 PM