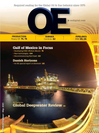
Page 79: of Offshore Engineer Magazine (May/Jun 2015)
Read this page in Pdf, Flash or Html5 edition of May/Jun 2015 Offshore Engineer Magazine
Eyebrow Production operations in the area.
amount of sand produced,
Up to 2012, Statoil had used a de- while shut-in means no sander during CT cleanout on C-19 that ? owrate because downhole took out about 50% of the sediments, but tubing is plugged with sand.
Historically, sand is han- the well was sending more sand, from
Making light work dled by locating a sand trap the wellbore, than the production facility at the entrance to the test could handle. In 2013, DualFlow was separator. This trap usually introduced, which routed the produc- handles 1-5% of total sand tion from the well to the DualFlow of sand removal production, corresponding unit. The ? owrate was then increased to 0.3-1.5 kg/hr of sand per to allow enough velocity and energy in well. the ? uid to lift the accumulated sedi-
Statoil’s well 34/10-C- ments from the wellbore. The DualFlow 19 at Gullfaks was drilled unit measured the accumulated solids, and completed in 1993/94, which were 20- 200 kilos/hr, depending and recompleted in 2002. on ? owrates. Online ? ushing of alternate
It was found that the sand cyclone vessels ensures the well remains rate rapidly exceeded the in constant production while being
A DualFlow system overview.
acceptable solids rate (ASR) cleaned. rates, pressure, temperature, and solids limit after clean-up, with well ? ow being Over the last two years, a total removed. Its dynamic range is 20 micron choked back. This occurred because the 15,000kg of solids has been removed to 5mm solids. Standard DualFlow units ? ow was too low to lift the sand up to the from C-19 alone. Two well bores were are rated to either 5000psi or 10,000psi as surface, to the topside-mounted separa- also being treated going to press. In total, required. tor, which would result in sand accumu- FourPhase has removed 37,000kg of sol-
The system, which weighs 8500kg and lating in the wellbore over time and a ids from 14 different wells from the start has a 200 x 200 x 328 cm footprint, has sand plug being formed. of the operation in Gullfaks.
a smaller footprint, at one third of the A sand clean-up is required once this In 2013, Wintershall took over the size of existing units on the market; uses happens. Conventionally, coiled tubing operatorship of Brage from Statoil.
Super Duplex piping and a carbon steel (CT), or snubbing, is used to establish However, a Brage well suffered badly frame; and is 99.8% ef? cient. FourPhase ? ow into a test separator. from solids production and was shut-in. also supplies its own X-Flow choke CT is run into the hole with a circulat- FourPhase mobilized early to kick-start manifold, which has directional control ing nozzle, going to the bottom and circu- the well and potentially be hooked-up and a reversible ? owpath. It can be used lating the solids. The CT is tied-in to the for further solids removal. The well for well clean-up or kick start applica- riser and connected into the DualFlow, was successfully kick-started and some tions or permanently installed in the to separate out the solids, and returning 7-tonnes of solids was removed from the production facility. either through the redundant Xmas Tree wellbore without CT or snubbing.
Production from the well is routed or tied directly into the test separator if FourPhase’s solids removal system to the DualFlow unit and the ? ow rate available. kick-started the blocked well without increased so as to allow enough velocity The test separator is not always acces- downhole intervention. The DualFlow and energy in the ? uid in order to lift the sible at the tie-in points. So FourPhase took out the solids upstream of any top- accumulated sand/? nes particles from has used the wellhead service wing side process units. The well is now the the wellbore. The weight of the accumu- with both master valves closed and the second-best producer on the whole ? eld, lated solids in the unit is typically 20-200 production wing open. Without coiled contributing to 10-11% of Brage’s total kilos/hr – ? owrate dependent. tubing, pressure support is needed in the production.
Norwegian energy giant Statoil chose reservoir to lift the solids.
Neil Meldrum is
FourPhase’s solution for the Gullfaks C But, using CT is a relatively expensive business development offshore installation, in the Norwegian process, costing some NOK 20-30 million manager at FourPhase.
Sea. Gullfaks started production in 1986. (approx. US$3-5 million), equivalent to
Before joining the
Initial recoverable reserves were esti- having a solids removal system on a rig company he held mated to be 2.1 billion bbl. for a whole year. Snubbing involves run- managerial positions
Production peaked at 605,000 b/d in ning the drill string on a pipe string using in product develop- 1994 and is now about 110,000 b/d, with a hydraulic workover rig at even greater ment, marketing and a 62% recovery rate. Intended production cost.
while production continues through the recovery is aimed at 74%, with part of A sand clean-up in Gullfaks’ C-19 had business development both in small second. The unit removes solids from this being achieved by using sand control been carried out almost every second technology companies and large integrated the production ? ow, by using centrifu- technology. year since it came online. The process service companies in the UK and interna-
Gullfaks C is known for its challenging gal forces internally to accelerate and also has disadvantages, including sand tionally. Prior to this, he gained ? eld and solids production, which has resulted in separate the sand, allowing a higher separation possibly being insuf? cient, operations experience in land seismic, reduced production rates due to well- production ? owrate, stopping solids a new CT rig having to be mounted permanent downhole monitoring and well bores having to be choked back and even accumulating either in the wellbore or for each well, having to send the sand testing. Meldrum gained an MSc in shut in. Choking back means having to production separator(s). It includes real- to shore for handling, and the clean-
Technology & Management in the Oil & Gas reduce wellbore ? owrate to reduce the time information logging, recording ? ow up operation con? icting with other
Industry from the University of Aberdeen.
oedigital.com May 2015 | OE 81 080_OE0515_ProdOps3_FourPhase.indd 81 4/20/15 6:19 PM