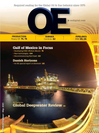
Page 84: of Offshore Engineer Magazine (May/Jun 2015)
Read this page in Pdf, Flash or Html5 edition of May/Jun 2015 Offshore Engineer Magazine
high-pressure jet (300-800 bar) generated by a Dynaset pump, in several stages.
In both cases, the ROV positioned the jet 1.5-2m from the subsea equipment,
Subsea and then gradually approached it to a
Putting hydrates distance of 50cm. The pressure from the jet could be adjusted by the ROV operator during cleaning up to a maximum level, which was set before the ROV was sent under high-pressure down. The highest pressure setting used was 500 bar, which is able to deal with nozzles to fnd the most effective design local sea water, to remove the hydrates, nearly all hydrate deposits.
While methanol/glycol for the job – a pointed nozzle proved bet- avoiding using chemicals. The company The nozzle was located at the end of cleaning could be considered ter at cleaning than one with a fatter end performed its frst water jet cleaning a “wand,” a rod attached to one of the the primary removal method, or a rotating nozzle. The nozzles were operation using the inspection, main- ROV’s robotic arms. At the same time the tested and demonstrated to the client tenance and repair vessel BOURBON ROV hung on to the subsea infrastructure its efciency in open water is before BOURBON personnel embarked Trieste, working with its ultra-heavy duty with is grabber arm. Precise indications limited. BOURBON has started on the operation. ROV. The job was done on a subsea Xmas on structure architecture were given by
The frst part of the operation involved tree in 1400m water depth offshore West the client, this meant the wand could be using high-pressure water jet using a low-pressure jet (10-20 bar) cre- Africa in 2013/14. controlled very precisely to clean even cleaning as an alternative. ated by a Zipjet pump, to remove the The project involved nearly two the most diffcult-to-access parts of the loosest layers of concretions. The remain- year’s preparation between the parties. equipment, accurately, safely and with ing hydrates were then removed using a BOURBON frst tested three types of no risk that the jet would damage it. emoving potentially consolidated hydrates from subsea infrastruc-
R ture is a concern for the oil and gas industry.
Hydrates are concretions, similar to “ice” in particular pressure and tempera- ture conditions, which can form on sub- sea infrastructure in deepwater. Hydrates can affect the operation of equipment by restricting movement of parts, so they need to be removed periodically.
Cleaning at these depths is carried out using heavy duty or ultra-heavy duty underwater remotely operated vehicles (ROVs), which most commonly apply methanol to dissolve the hydrates. While this can be highly effective, methanol treatment has its disadvantages.
This primary method for cleaning involves pumping the methanol from a foating production system, and diverting the subsea injection point by re-routing piping and installation hoses to “attack” the subsea equipment.
An entire cleaning operation might require more than 10-20,000 liters of methanol, because the effectiveness of using methanol when cleaning the exterior of equipment is reduced by the diluting effect of the seawater.
Due to the volume required, the injec- tion of methanol directly from an ROV- borne skid, typically containing 15 gal bladders, was disregarded.
BOURBON has developed a method using a high-pressure water jet, using
The lifting the BOURBON Trieste
Schilling heavy duty work class ROV.
Images from BOURBON.
May 2015 | OE oedigital.com 86 086_OE0515_Subsea Bourbon.indd 86 4/20/15 8:32 PM