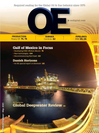
Page 85: of Offshore Engineer Magazine (May/Jun 2015)
Read this page in Pdf, Flash or Html5 edition of May/Jun 2015 Offshore Engineer Magazine
high-pressure jet (300-800 bar) generated During this entire process, the client environmental risks and time savings,
SubseaEyebrow by a Dynaset pump, in several stages. was also able to follow the operation due to operators being more familiar with
In both cases, the ROV positioned the from the FPSO in real time by viewing methanol cleaning, which is perceived as jet 1.5-2m from the subsea equipment, the images from the video cameras on being less risky for the subsea assets. and then gradually approached it to a the ROV. That meant the client was able A growing track record of success, distance of 50cm. The pressure from the to provide instructions, verify that the improved knowledge and technological jet could be adjusted by the ROV operator operation was progressing smoothly and advances are likely to promote wider during cleaning up to a maximum level, call a halt if they had concerns – or when use of the water jetting technique in the which was set before the ROV was sent they were satisfed that the cleaning pro- future.
down. The highest pressure setting used cess had met their requirements. Field operators could also adopt a was 500 bar, which is able to deal with The operation removed all of the hybrid approach to hydrates cleaning if nozzles to fnd the most effective design nearly all hydrate deposits. hydrates, while protecting the lines they remain concerned about the risks, for the job – a pointed nozzle proved bet- The nozzle was located at the end of and cables on the structure. Since then, using high-pressure jets to complete ter at cleaning than one with a fatter end a “wand,” a rod attached to one of the BOURBON has successfully carried out the bulk of the cleaning process and or a rotating nozzle. The nozzles were ROV’s robotic arms. At the same time the this cleaning process several more times then turning to methanol cleaning for tested and demonstrated to the client ROV hung on to the subsea infrastructure for the same client. The frequency of the most sensitive areas of the subsea before BOURBON personnel embarked with is grabber arm. Precise indications such operation depends on the density of infrastructure.
Whatever technique is used, removing on the operation. on structure architecture were given by shallow gas in the seabed. hydrates is a delicate business. But, as
The frst part of the operation involved the client, this meant the wand could be While the project was a success, it is confdence in the ability of ROV operators using a low-pressure jet (10-20 bar) cre- controlled very precisely to clean even unlikely that the technique will com- to use high-pressure jets grows, the estab- ated by a Zipjet pump, to remove the the most diffcult-to-access parts of the pletely replace low pressure methanol lished trend towards greater use of this loosest layers of concretions. The remain- equipment, accurately, safely and with cleaning across the oil and gas industry method will only become stronger. ing hydrates were then removed using a no risk that the jet would damage it. in the near term, despite the lower cost,
Operations underway in the deep.
oedigital.com May 2015 | OE 87 086_OE0515_Subsea Bourbon.indd 87 4/20/15 8:33 PM