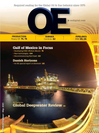
Page 88: of Offshore Engineer Magazine (May/Jun 2015)
Read this page in Pdf, Flash or Html5 edition of May/Jun 2015 Offshore Engineer Magazine
Pipelines allowance and introduction of
Plastic a corrosion inhibitor into the product. and technical benefts. These However, for ambient water injection developments have been driven service, the application of a polymer lin- by both industry and consultan- ing system is now becoming the bench- fantastic cies, in an effort to achieve wider mark. Where water injection service understanding of the signifcant requirements are more extreme and in
Polymer-lined pipe has been benefts that polymers bring. hot sour hydrocarbon service environ- around since the 1990s, but ments, corrosion resistant allow (CRA)
Lined pipelines and the lining and cladding, or even a solid CRA, its potential has yet to be traditional alternatives is commonly specifed to handle the cor- fully tapped, according to
Pipelines typically form a major rosive nature of the transported product. those behind JIPs to extend proportion of the development This method, however, has signifcant cost of a subsea project, particu- implications on the procurement, sched- use of this technology. larly for long subsea tie-backs. uling and installation costs of a subsea
Mostafa Tantawi and David
Polymer liner insertion
The costs, which include pro- pipeline.
into carbon steel pipe.
Whittle explain. curement, fabrication and instal-
Polymer lining lation, are mainly driven by the pipeline material selected and method of assets. Key to addressing these chal- he UK oil and gas industry is in Polymer lining technology was intro- installation. lenges is innovation, and investment into the midst of some troublesome duced to the oil and gas subsea sector in
T
A signifcant part of the cost of main- research and development must continue times. The new, lower price of the mid-1990s. Installation is achieved taining a subsea pipeline is incurred to help maximize the recovery of remain- Brent oil, averaging US$45-60/bbl dur- by pulling an extruded polymer pipe attempting to combat internal corrosion. ing hydrocarbon reserves. ing the last six months, has seen drastic through a reduction die to temporar-
Carbon steel is traditionally selected for Extensive research and develop- measures taken to make cost savings and ily reduce its diameter. While in this the fabrication of risers and fowlines, ment has gone into developing pipeline reduce operational spend. reduced state, the pipe continues to be with protection from corrosion and ero- polymer lining solutions, which have Operators are being challenged to pulled through the constructed carbon sion afforded by the “thickening” of the the potential to offer considerable cost investigate new ways of implementing steel carrier (outer) pipe, before being pipe, through the addition of a corrosion savings as well as signifcant operational cost reductions to oil and gas producing released and reinstated to its initial size
May 2015 | OE oedigital.com 90 090_OE0515_Pipelines2_Polymer_JIP.indd 90 4/20/15 9:04 PM