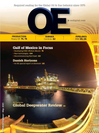
Page 89: of Offshore Engineer Magazine (May/Jun 2015)
Read this page in Pdf, Flash or Html5 edition of May/Jun 2015 Offshore Engineer Magazine
Pipelines considered as an option.
Technical overview
The technical bene? ts of plastic lined pipelines are vast. Polymers are corrosion resistant, which immediately negates the need for corrosion inhibitors throughout the life of the pipeline or the requirement of a CRA derived pipeline.
Polymer liners are currently favored in the majority of subsea water injection pipelines in the North Sea due to the cost effective corrosion resistance and reliability, with a signi? cant increase in the number of operators recognizing the technology in recent years.
Polymer lining can also allow for potential unprocessed (production) water re-injection service, which saves on the requirement for topside de-aeration equipment. With an increased need for hotter water injection temperatures, different types of higher performing poly- mer materials are now available to ful? l varying service requirements.
Butt fusion welding of polymer pipe.
Photos from Swagelining.
Until now, high performance grades of so that it ? ts tightly to the host. Lengths polyethylene, predominantly polyethyl-
Senior development engineer of liner up to 1500m have been installed ene (PE) 100 have been used for the vast from Swagelining Limited’s in single operations. majority of lining applications. PE 100 is
Technical Development Group
Following the completion of this inser- suitable for use in water injection service machining the polymer lining to tion process, bespoke ? angeless connec- up to 60°C, where long lifetimes can be accept connector technology.
tor technology is used to join together expected in the relatively benign condi- lined pipe sections at the ? eld joints. tions of treated seawater for example. allowance and introduction of Polymer-lined subsea pipelines are At higher temperatures, up to 85°C, a corrosion inhibitor into the traditionally installed by reel lay, J-lay and where an option for produced product. and in bundles. Existing connector water re-injection may be required, a and technical bene? ts. These However, for ambient water injection technology restrictions have excluded more chemically resistant polyethylene developments have been driven service, the application of a polymer lin- the application by S-lay until now, but such as PE-RT (polyethylene of raised by both industry and consultan- ing system is now becoming the bench- new developments are allowing this to be temperature resistance) can be used. cies, in an effort to achieve wider mark. Where water injection service 60 understanding of the signi? cant requirements are more extreme and in bene? ts that polymers bring. hot sour hydrocarbon service environ-
External insulation (5LPP)
Internal insulation (15mm PVDF) ments, corrosion resistant allow (CRA) 55
Lined pipelines and the lining and cladding, or even a solid CRA, traditional alternatives is commonly speci? ed to handle the cor-
Pipelines typically form a major rosive nature of the transported product. 50 proportion of the development This method, however, has signi? cant cost of a subsea project, particu- implications on the procurement, sched- larly for long subsea tie-backs. uling and installation costs of a subsea 45
The costs, which include pro- pipeline.
curement, fabrication and instal-
Temperature (C°) 40
Polymer lining lation, are mainly driven by the pipeline material selected and method of Polymer lining technology was intro- installation. duced to the oil and gas subsea sector in 35
A signi? cant part of the cost of main- the mid-1990s. Installation is achieved taining a subsea pipeline is incurred by pulling an extruded polymer pipe attempting to combat internal corrosion. through a reduction die to temporar- 30 0510 15 20 25 30 35 40 45
Carbon steel is traditionally selected for ily reduce its diameter. While in this
Total distance (km) the fabrication of risers and ? owlines, reduced state, the pipe continues to be with protection from corrosion and ero- pulled through the constructed carbon
Indicative example of steel temperature for external 5LPP system vs. 15mm PVDF Indicative example of steel temperature for external 5LPP system vs. 15mm PVDF sion afforded by the “thickening” of the steel carrier (outer) pipe, before being internal liner (based on case study conducted by Xodus Group Ltd. Inlet ? uid temperature = 60°C) Graphs from Xodus.
pipe, through the addition of a corrosion released and reinstated to its initial size oedigital.com May 2015 | OE 91 090_OE0515_Pipelines2_Polymer_JIP.indd 91 4/20/15 9:05 PM