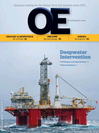
Page 37: of Offshore Engineer Magazine (Aug/Sep 2015)
Read this page in Pdf, Flash or Html5 edition of Aug/Sep 2015 Offshore Engineer Magazine
interfering with other systems, pipelines operation, and ease of building and Embedding constructability into the
EPIC and components. installation. design process requires the use of 3D and
Getting constructability wrong can This can be achieved by running a 4D modeling tools, such as Autodesk have dramatic consequences for sched- constructability study in parallel with the Navisworks and 4D-BIM. 3D modeling ules, costs, quality of installations, the design activities, so that constructability software can be fed with information ability to remediate defects or construc- is considered at each phase of detailed related to both physical clashes and the tion errors, safety and possibly cause design. This process will cover turret space allowances necessary for installa- the need to dismantle mechanically fabrication, commissioning and testing, tion and maintenance operations and, completed systems to allow completion, and lead to better overall time keeping, with the addition of 4D modeling, sched- testing or repair of other systems. lower costs and higher quality products uling clashes.
For example, in some industry situ- for the project with a better construction
Design criteria ations, the fange sealing face of large safety record.
components such as valves were dam- Constructability studies should Each project also requires its own crite- aged during installation due to poor include: ria, such as deck-framing plans designed • access or inadequate lifting facilities. Challenging each proposal at the design and placed to support components in
As a consequence, the following helium stage in terms of fabrication, installation place as well as to temporarily support leak test failed and the only solution was and testing. them during installation and replace- • to rework the fange face by machining. Identifying fabrication, installation ment, or suitable spaces between compo-
That meant that, in the restricted space, and testing methods and techniques to nents to allow for installation, replace- the installation of the milling machine improve the construction sequence and ment and maintenance. Another criteria necessitated a large section of the adjoin- avoid any need for reworking. could be that lifting facilities, covering • ing piping and related instrumentation Detailing the construction sequence to the external and internal areas of the to be dismantled. The high-pressure give the best possible option for install- turret, are provided and drop-pick areas are accessible to all lift- ing equipment. Detailed design should focus on items necessary for easy installation by avoid- ing the need for extra construction resources, such as highly specialized workmanship or extra lift- ing equipment.
Inspection strategies and methods must be built into the design criteria. It is useless to build a tur- ret if technicians cannot access it in order to test and inspect it later.
Further detailed design issues that should be built into the 3D modeling modeling capable of optimizing spaces process are: • and preventing physical clashes, such Ensure components, solutions might not take into account including valves, mani- how easy and practical it is to build, folds and large piping install and test the turret. A good design, spools, are equipped with which will work well in service, could permanent or removable be slow, costly and diffcult to fabricate, legs, pedestals, saddles install and test. and lifting points or lugs
Italian classifcation society RINA is suitable to lift, slide, bal-
FSRU . Toscana Photos from RINA.
advocating including “constructability” ance and level as neces- as a design criteria. Constructability is leak test failure introduced an unwanted ing components and limiting conficts of sary the components during installation, the ease and effciency of fabricating, safety issue, delay to the schedule, and disciplines and the need for rework. positioning and ftting-up with adjoining • installing and testing the main process an overall lower quality outcome because Identifying and quantifying the mini- piping.
• piping lines, subject to the design and brand new items had to be repaired mum requirements of resources such as Ensure deck areas are equipped with integrity requirements of the installation. before startup. specialized workmanship, equipment, lifting facilities capable of linear over-
The philosophy behind constructabil- materials and consumables. head handling and maneuvering heavy
Striking a balance • ity is to ensure that each system, pipeline Verifying the availability of resources to components from the drop-pick area to and component can be installed and There is a balance to be struck between meet the schedule and drafting contin- directly over the support or saddle. • tested in a scheduled sequence without simplicity of design, effciency of gency plans as applicable. Ensure decks are equipped with foor oedigital.com August 2015 | OE 39 038_OE0815_EPIC1_rina.indd 39 7/21/15 7:38 PM