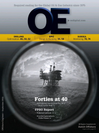
Page 33: of Offshore Engineer Magazine (Sep/Oct 2015)
Read this page in Pdf, Flash or Html5 edition of Sep/Oct 2015 Offshore Engineer Magazine
before a discovery was even made. Part of this was due to the the scrubbers before pumping it into the gas export pipeline. fact that the 20 or so deepwater leases acquired for production by This approach would effectively eliminate the recycle loop and
LLOG in 2010 were set to expire in early 2014 – requiring expe- reduce compression requirements, but a lower volume of sales dition of the entire construction process so that the FPS could be oil would be produced.
brought online and wells could be drilled within 36 months. The second option included a complete overhaul of the
In order to achieve this milestone and keep pace with the original design by replacing much of the topsides equipment highly aggressive production schedule, topsides engineering con- with a crude stabilizer. This would enhance separation of tractor Audubon Engineering Solutions had to begin front-end the condensates, reduce compression, and allow RVP speci- engineering design (FEED) efforts before reservoir characteristics ? cations to be met. The process itself, however, was overly were de? ned. complex and required a great deal of heat in order to operate.
Assuming a reservoir composition similar to a nearby analo- The necessary equipment presented structural concern due to gous ? eld (GOR of ~2000 scf/bbl and 28-32°API), the initial its weight as well. design included routing liquids from compressor scrubbers During the process of evaluating these options, efforts were to production separators with lower operating pressures – a made to replicate the data from the initial PVT analysis in a method commonly used on offshore facilities to reduce liquid process simulator. When it could not be done, a second analysis recycle and minimize compression requirements. was ordered to con? rm the suspicion that the data was incorrect.
During this initial design process, however, a well sample As expected, the second analysis revealed that the reservoir com- phase behavior (pressure, volume, temperature or PVT) analysis position was in fact much closer to what was originally assumed conducted by a third-party laboratory revealed that the reser- (stock GOR and speci? c gravity were calculated to be ~2100 scf/ voir contained a stock GOR of approximately 2300 scf/bbl and bbl and 37°, respectively). This data was more favorable from a a crude oil gravity of 38°API – a substantial deviation from the processing standpoint, but with relatively high amounts of con- previously assumed composition. The analysis also indicated densate still detected, the large recycle loop remained. that reservoir ? uid was rich in condensates, including propane After the new PVT data was veri? ed in a process simula- (C3), butane (C4), and pentane (C5), resulting in a much larger tor, the total overhaul of topsides equipment and addition of a liquid recycle and higher compression requirements in order crude stabilizer was taken off the table. The option of adding a to meet oil pipeline Reid vapor pressure (RVP) speci? cations. condensate processing train by itself was also reconsidered due
Although Audubon Engineering Solutions and LLOG were to its inability to provide adequate separation. After examin- suspicious whether this data was entirely accurate, given the ing different seasonal and environmental conditions in order unusual numbers, they proceeded under that assumption that if to better understand how the facility would operate throughout it were even remotely indicative of the reservoir’s composition, the year, it was determined by LLOG and Audubon Engineering a conventional liquids handling philosophy would be impracti- Solutions that a hybrid of these two options would be most cal and other options would need to be explored. appropriate given the unique composition of the ? eld.
Delta House. Image from LLOG Exploration Co.
Liquid handling options The solution: condensate stabilization
When considering a new liquid handling design approach, two The new hybrid design for liquid handling at Delta House options were examined. The ? rst option was to retain much of included keeping most of the equipment from the initial FEED the equipment used in the original design and add a conden- phase – along with the condensate processing train – and adding sate processing train in order to dehydrate the condensate from a stabilizer with overhead cooling and two-phase separation of
Fig. 1: Simpli? ed ? ow diagram of the condensate
To compression stabilization system
Coalescing Overhead
To compression ?lters condenser
Overhead separator
From
To sales
FGC scrubbers
NGL
Condensate
Freewater
Charge pumps &
Stabilizer knockout pipeline pumps
Reboiler
To LP SEP
Bottom
To LP SEP
Cooler
Stabilized condensate oedigital.com September 2015 | OEoedigital.com September 2015 | OE 3535 034_OE0915_Feat3_Audubon.indd 35 8/19/15 8:02 PM