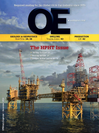
Page 29: of Offshore Engineer Magazine (Dec/Jan 2015)
Read this page in Pdf, Flash or Html5 edition of Dec/Jan 2015 Offshore Engineer Magazine
heat generated or experienced by an affected umbilical can lead to accepted temperature limits being exceeded for commonly used umbilical materials, resulting in de-rating of stress allow- ances or corrosion of metallic compo- nents, and mechanical degradation of polymers.
These factors leave umbilical manu- facturers faced with many challenges; how do we design umbilicals to with- stand these temperatures? Can these materials last for 25 years in service?
Will new products be more cost ef? cient
Hose end ? tting. than current designs?
Facing these challenges led Technip
Umbilicals to undertake several research 100
DUCO?ex HT retains and development initiatives on new properties at elevated technologies to ensure we can create temperature products that are not only high quality but are also cost ef? cient for the current market.
DUCO?ex HT @ 40° C
Change in
DUCO?ex
Overcoming challenges
DUCO?ex HT @ 80° C properties at
Materials used within traditional elevated
DUCO?ex @ 40° C thermoplastic umbilicals are able to temperature 50 cope in a wide range of applications and
DUCO?ex @ 80° C environments, including low-temperature
Loss in Polyamide properties due
Polyamide @ 40° C and long-term continuous operations. to elevated
However, using these materials in high- temperature
Polyamide @ 80° C temperature environments, especially over long periods of time, can result in issues including; reduced collapse resis-
Retained mechanical properties (%) tance due to material softening, reduced service life from degradation and dif- ? cultly in retaining the coupling on the 0 0 1 2 3 4 5 end of the hose. In order to give the prod-
Aging duration (years) uct long term viability, a fundamental
Figure 1 – Traditional hose liner materials vs. DUCO? ex HT.
change in all aspects of the hose design from liner material, reinforcement mate- and collapse resistance. At the outset of this development, rial, cover material and end ? tting design was required.
a range of materials were evaluated in order to determine
To overcome the high temperature concerns in hose technol- the optimal material for high temperature environments, ogy, Technip Umbilicals has developed a new thermoplastic whilst maintaining the proven advantageous properties of hose design known as DUCOFlex HT (high temperature), creat-
DUCO? ex.
ing a product which can operate continuously at temperatures from -40°C to +80°C and is capable of sustaining intermittent In order to determine the long-term suitability of candidate use at temperatures from -50°C to +100°C for longer periods of materials, samples of Technip Umbilicals’ traditional hose time, ensuring no degradation in performance. liner materials and the proposed new DUCO? ex HT material
Any new material must be more cost effective for future were exposed to synthetic seawater at various temperatures for developments compared to the alternative; super duplex stain- durations up to ? ve years, and as can be seen in Figure 1. It is less steel tubes or coated tubes, which have a higher component clear that the new DUCO? ex HT hose material retains struc- and manufacturing cost compare to standard thermoplastic tural integrity during long term exposure to high temperatures, hose. Also, the additional bene? ts from easier termination and whereas the common alternatives, especially polyamide rapidly installation of thermoplastic umbilicals compared to steel tube loose mechanical strength, resulting in signi? cantly shorter life umbilicals needs to be preserved to ensure the overall cost and reduced collapse resistance. advantage is maintained. The increased temperature performance of the new DUCO? ex
HT hose also results in a more stable ? exural modulus value
Bene? ts of the technology as the temperature increases, this means that not only does the
Technip Umbilicals patented the use of the polyethylene comparative collapse performance of the hose increase for a based liner technology DUCO? ex in 1994, which gave signi? - given temperature, it retains collapse performance over a sig- cant performance improvements in terms of ? uid permeation ni? cantly greater temperature band, meaning the useable water oedigital.com December 2015 | OE 31 030_OE1215_HPHT2_Technip.indd 31 11/21/15 1:33 PM