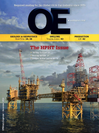
Page 30: of Offshore Engineer Magazine (Dec/Jan 2015)
Read this page in Pdf, Flash or Html5 edition of Dec/Jan 2015 Offshore Engineer Magazine
HPHT with standard JIC or metric adaptors. However, as with traditional ftting designs, alternative joining arrangements can be provided to suit the clients’ requirements including stub pipe designs for welded terminations to remove any threaded seal interface.
Going ofshore
To reinforce the fndings from research, a recent tender case study for high-temperature umbilicals focused on a 6km-long umbilical project located in 100-200 m water depth within Asia Pacifc. The study highlighted that during planned mainte- nance the annulus lines were bled down via a vent line in the umbilical, allowing hot fuid to fow through and heat up the umbilical. During a typi- cal operation, depending upon the water depth, constituency and temperature of the fuid, this could reduce the collapse resistance and limit the design life of a standard hose design. Traditionally this would have meant the hose was replaced with a stainless steel tube (lean duplex or super duplex), but this increases the cost and complexity of the umbilical. The steel tube is generally a longer lead time item, has higher bending stiffness, requires more time and cost to ft end terminations, is more challenging to install, has a fnite fatigue life and is more costly especially if a corrosion protec- tion coating (fusion bonded epoxy, for example) is required. By substituting steel tube with a new high temperature hose design this signifcantly increases the temperature and water depth per- formance without the costs and disadvantages of steel tube and enables the umbilical to remain fully thermoplastic with all of the associated benefts.
For this project study, a saving in the region of 10% was made by not replacing the affected hose with a super duplex stainless steel tube. Further
Thermoplastic hose. Photos from Technip.
savings could be realised through simpler termina- tion hardware and less complex installation. depth is signifcantly increased also.
Taking umbilicals further
The hose reinforcement design, both in terms of material and
In the current market conditions, it is extremely important specifc construction, has been modifed to give enhanced long that companies adapt their products to fulfll market needs term performance at higher temperatures and has been tuned to but with a strong focus on cost optimisation. As subsea mar- give an optimal performance balance between working pres- ket demands change, Technip Umbilicals are meeting these sure rating and impulse fatigue. These modifcations ensure the challenges with cost effective, industry leading products. hose technical performance is improved, but critically remains fully ISO compliant, including a 4:1 factor of safety on burst pressure. Alan Rutherford has been working at
The metallic end fttings utilized with high-pressure
Technip Umbilicals for over 15 years, umbilical hoses are typically the most challenging element during which time he has worked on in what is a very robust system. Therefore, in addition to various research and development projects the material changes to the hose construction, a new style including Super Duplex steel tube fatigue of ftting needed to be developed to guarantee successful and long term ageing of materials. service at the higher temperatures. Elements of this
Rutherford is currently a principal engineer ftting have been patented including a secondary lock nut and lead of the team responsible for mechanism to mitigate against loosening of the ftting during research and development of hose products and thermoplastic service. This ftting has been developed to allow connection materials used within umbilicals.
December 2015 | OE oedigital.com 32 030_OE1215_HPHT2_Technip.indd 32 11/21/15 1:34 PM