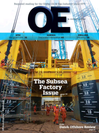
Page 26: of Offshore Engineer Magazine (Aug/Sep 2016)
Read this page in Pdf, Flash or Html5 edition of Aug/Sep 2016 Offshore Engineer Magazine
SUBSEA FACTORY the North Sea and West Africa due to the water depths, reservoir char- acteristics and tie back distances.
Subsea gas compression projects require somewhat larger resource base than the booster pumps, in or- der to be commercial. Key regions for this technology over the next coming years will likely be the
North Sea, Australia, East Africa and the Mediterranean. Subsea separation systems have now been installed at 11 ? elds operated by
Petrobras, Statoil, Shell and Total.
All the ? elds lay in Brazil, Norway,
US GoM or Angola, and going for- ward these areas, including the rest of the North Sea and West
Africa, are seen as the primary markets for such systems.
An illustraton of the the wet gas compressor meant for the Gullfaks South subsea factory.
Considering the number of sub-
Illustration from Statoil.
sea ? elds (~1500) compared to the number of subsea boosting (~40), 3000 compression projects (2) and subsea separation (11) systems,
Perdido 2500 the current technology adoption is low. The main reasons for this
Parque das Conchas Parque das Conchas (x-BC-10) Phase 1 (x-BC-10) Phase 2 2000 are related to costs, uncertainty regarding reliability (proven on boosting and separation by now), 1500 and a general conservatism in the industry. In the current low price
Marlim 1000 oil environment, we have seen
Paz?or clear signs that operators are
Troll Pilot 500
Corvina
Tordis looking into how to increase the
Congro
Marimba production from existing ? elds
Malhado 0 1990 1995 20002005 2010 2015 2020 to improve cash ? ows short/ medium term. In some instances,
Figure 2: Subsea separation projects by water depth (meters) and installation year. the operator may prioritize such
Source: Rystad Energy.
projects, over green? eld develop- delivered the Åsgard project, which includes pre-compression ments, due to a lower overall capex and time to production. separation, while OneSubsea delivered the system for Gullfaks Due to this, the current downturn may yield an increase
South. The Gullfaks South project has had some initial problems, in subsea processing projects for brown? eld applications. but the Åsgard system has so far run like clockwork. Although Brown? eld processing could be some of the more interesting somewhat costly projects, part of the costs should probably be projects before green? eld sanctioning picks up with an esti- allocated to research and development, and thus, future systems mated recovery in the oil price towards 2020. are likely to be considerably cheaper.
Subsea separation is the concept of separating gas/liquids Jon Fredrik joined Rystad Energy in 2010. or oil/water at the seabed, and might in some instances be a Before that, he worked as a consultant at prerequisite for other subsea processing systems. Many of the Accenture. His area of expertise includes applications so far have been in conjunction with subsea booster strategy and market assessments, macro pumps, and subsea separation is today a proven technology. analysis, transaction support and
While OneSubsea has taken the largest share of the booster mar- valuation for upstream E&P, oil? eld ket, it is FMC Technologies that has become the market leader in services, ? nancial institutions and the separation segment, being system provider on the majority governments. He holds an M.Sc. in of projects completed, see ? gure 2. Industrial Economics and Technology Management from
Booster pumps are mainly used on oil ? elds with low gas to NTNU, Norway and participated in a graduate exchange oil ratios, both for heavier and lighter crudes. The key regions program at the Haskayne School of Business, University of have been, and will continue to be, Brazil, the US Gulf of Mexico, Calgary.
August 2016 | OE oedigital.com 28 026_OE0816_Feat3_Rystad.indd 28 7/25/16 12:10 PM