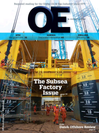
Page 57: of Offshore Engineer Magazine (Aug/Sep 2016)
Read this page in Pdf, Flash or Html5 edition of Aug/Sep 2016 Offshore Engineer Magazine
change that could impact on someone • Kongsberg Maritime: Vessel order to make the interface work.
DRILLING else’s systems without knowing.” Management System/Safety systems: This gave Songa Offshore far greater
Patrick Rossi, DNV GL ISDS project Power management systems (PMS) plus control over supplied software. Standard manager for Cat-D comments: “Tracking dynamic positioning plus ? re and gas supplier software change management tools enabled by ISDS can also be used plus Emergency shut-down systems = 32 procedures were improved, more soft- for decision making and staf? ng of PLCs and several Microsoft Windows- ware faults were identi? ed before their needed software resources for approval based operator stations usual discovery phase during operations, • and validation of changes.” ABB: Drilling and thruster variable and tracking the status of software de-
As software is often un? nished when frequency drives (VFDs) = 21 PLCs and sign documents was much easier. “It [ISDS] also helps in the future when systems are delivered to the yard, inter- 9 Microsoft-based systems we come to test anything we can show this faces are not always completely engi- “All of the above PLCs and computers is where we were at that point in time and neered or tested, so software interfaces also come with manufacturer’s ? rmware how we got there. If there are any changes, need to be coordinated at the vessel level.
(which is low level manufacturer soft-
Software updates are also always hap- we can go back to the last point we know ware), so actually there are more sources pening during construction: tuning, bug it was all working,” Coward says. of software to be aware of,” Rossi says.
“Should there be an accident or some ? xes, changes to software requirements
Implementation equipment damaged, the ? rst thing (thousands of changes on hundreds of
ISDS implementation on the Cat-D rigs anyone wants is to go back to a base line different programmable logic controllers was done in such a way that as each new that would show everything has been (PLCs) and computers); so the tracking rig was rolled out, learnings from the tested and working. In the past, that and timely (successful) testing of integrat- last rig were transferred to the next rig, would be delivery.“If we changed some- ed software systems is a real challenge.
The original manufacturer of the and as new learnings were introduced thing on the fourth rig, we ensured that equipment also sometimes sends in each new rig, they were in turn rolled we followed through on the third, sec- updates to their ? rmware that are not out across the previously built rigs. ond and ? rst rigs,” he says. In fact, the requested by the project and may cause Initially, the ISDS scope hadn’t in- system is designed so that any change unstable conditions and problems dur- cluded the main engines, but this was made, if it’s applicable to previous ves- ing construction and commissioning, if brought into the system as it was seen as sels, needs to be rolled out to the other they are not coordinated and planned. being a mistake not to include them. vessels before the task can be closed out.
Furthermore, software is not always
The result is a ? eet working on the This means that you don’t end up properly addressed during design/reli- same version software systems and with four rigs each with their own sys- ability analysis; ISDS RAMS require- shorter commissioning time, Coward tems,” Coward says. “It is a lot of work, highlight the need for software says. “It has been hard work but it has without a doubt. With so many vendors ments and track the outcomes of failure focus been worthwhile,” he says. interfacing with each other, it was a lot th throughout the project. The list of modes
With ISDS, all the software systems of work and we took it to the n degree. ed software systems onboard the integrat are tracked, during the build, commis- But it has de? nitely been a bene? t.” “A tremendous amount of work by an
Cat-Ds helps illustrate the complexity sioning and post commissioning so that entire dedicated team preparing all of involved: the current as well as any past setup can • Aker Solutions: Drilling Control be seen. the rigs for Norway was done to ensure
System (DCS): Tool pusher and driller Having the documentation which a timely acceptance phase; many things control panels plus anti-collision = 35 shows which version of software is can go wrong and having ready, stable, programmable logic controllers (PLCs), being used at any one time means that completed software also plays a key role. several servers and industrial computers during the build, if an interface isn’t
For CAT-D the acceptance phase was com- and HMI software. working, it is easier to tell a particular pleted in four weeks which is a noticeable • Cameron: Well control: Blowout pre- manufacturer or vendor what version of achievement for such sophisticated rigs.” venter (BOP) plus diverter/HPU = 9 PLCs software they need to comply with in says Mark Bessell, Songa COO.
Overview of ISDS (December-2012 version)
Songa Equinox
Lifecycle of ?ve phases:
A B C D E
Basic
Engineering Construction Acceptance Operation
Engineering
M1 M2 M3 M4 M5
Fourroles:
Owner System integrator Supplier Independent veri?er
Three con?dence levels: 11 process areas, 119 activities
Reliability, Availability, Maintainability and Safety (RAMS)
CL1 CL2 CL3
Design validation
Integration engineering
Requirements
Veri?cation and
Implementation
Con?guration management
Acquisition
Supporting
Process and quality assurance process areas
Project management
Risk management
ISDS process overview. Image from DNV GL.
oedigital.com August 2016 | OE 59 058_OE0816_D&C1_DNV Songa.indd 59 7/24/16 10:58 AM