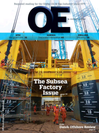
Page 58: of Offshore Engineer Magazine (Aug/Sep 2016)
Read this page in Pdf, Flash or Html5 edition of Aug/Sep 2016 Offshore Engineer Magazine
Using wired drill pipe
DRILLING to drive down well cost
Drill ? oor operations. Photo from NOV IntelliServ.
in the bottomhole assembly (BHA) will often see this time occur. This could be during surveys, on connection or mid- stand, during check/roll surveys, while downlinking off-bottom or shallow hole testing, during pressure testing, forma- tion integrity testing, leakoff testing, signal trouble shooting, etc.
Although individually these instanc- es makeup a small time component, once accumulated across an entire well, this value can add up to multiple hours or even days. Oil major Total, in Norway, recently published telemetry time reduction results (ref: SPE 178863, 2016) that it realized from implementing WDP in its operations at the Martin Linge ? eld, where there was a 82% reduction in normalized telemetry time per well.
Wired drill pipe has been a long time coming. As operators
WDP offers other bene? ts, including look at cost savings across the full life cycle, the bene? ts increasing rate of penetration (ROP) through high frequency, low latency are now being recognized, says NOV’s Leon Hennessy. downhole data, allowing real-time ired drill pipe (WDP) is placed every 1500ft along the drill string, optimization, and enhanced real-time conventional drill pipe clean and boost the data signal for optimal visualization and monitoring of equiva-
W modi? ed to accommodate signal-to-noise ratio along the network. lent circulation density. These bene? ts an inductive coil embedded in the The main bene? t of WDP is to enable a can be enhanced further with the use secondary shoulder of both the pin and reduction in telemetry related ? at time, of along-string measurements includ- box end. These coils are connected via i.e. any time that is spent off-bottom ing pressure measurements, to manage an armored, high-strength DataCable waiting on mud pulse telemetry to send wellbore conditioning and time spent embedded inside each tool joint, a signal to surface. Any drilling opera- circulating off bottom. Real-time data enabling high-speed downhole data to tion using measurement while drilling can help improve well placement and be transmitted across the drill string. (MWD), logging while drilling (LWD) geo-steering on-the-? y and reduce un-
DataLink sub-assemblies, typically or rotary steerable systems (RSS) tools planned bit and BHA runs by detecting
Figure 1 – Well A Telemetry Time Savings Figure 2 – Well B Telemetry Time Savings
Analysis (hours) Analysis (hours) 35 Relogging MWD 20 1.23
Fit / LOT 30 3.15 6.18
MPT signal testing 15 25
ESD
Pressure testing / FPWD 1.88
MPT signal testing 20 13.48
Ranging 1.14 10
Downlink to RSS tool
Downlink to RSS tool 1.42 15 0.85 (o