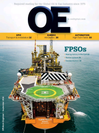
Page 21: of Offshore Engineer Magazine (Sep/Oct 2016)
Read this page in Pdf, Flash or Html5 edition of Sep/Oct 2016 Offshore Engineer Magazine
Firsts • Turritella is the ? rst FPSO used by Shell in the Gulf of Mexico • The deepest ? oating production unit in the world
The largest disconnectable • buoy
The ? rst disconnectable FPSO • with steel lazy-wave risers in
Aerial views of the FPSO while docked at Keppel’s yard. Turritella Photos from Shell.
Breaking ultra-deepwater how to safely shut down operations and get people out of phase comprising two subsea production wells tied back to harm’s way. This was one factor that led Shell to choose a the Turritella FPSO. In all, there will be eight wells connected disconnectable FPSO for the project. Another factor, Lohr back to the FPSO. Shell expects to add six wells, in later phas- said, was the ? exibility to disconnect and leave in the event es after ? rst oil, with multiphase pumping. The eight wells of extreme weather, but to also not have to use an oil export will be connected to the FPSO through two drill centers. The pipeline. reservoir depth is around 26,500ft (8077m) below sea level and “The advantage of using a FPSO for this frontier project 17,000ft (5181m) below the mudline.
is the ? exibility that it gives Shell –to learn more about this In October 2015, Technip was awarded the contract for the reservoir and grow accordingly,” Lohr says. “Stones is a re- development of subsea infrastructure for Stones that includes ally exciting prospect for Shell. It could turn out that it is two subsea production tiebacks to the FPSO, in addition to an extremely large ? nd, but we won’t know until we start engineering of the second pipeline end terminations (PLETs); producing.” fabrication of the PLETs and piles; and installation of the
According to SBM Offshore’s Turritella factsheet, released subsea production system, inclusive of associated project this May, the disconnectable capability allows the FPSO to management, engineering and stalk fabrication.
not only quickly and safely sail away in the event of a hurri- In August last year, OneSubsea landed a contract to supply cane, but also quickly resume production once the hurricane subsea processing systems, which includes a dual pump sta- has passed the location, which Shell highlighted as an impor- tion with two 3MW single-phase pumps and two subsea con- tant factor for productivity at the ? eld. trol modules, a topside power and control module, a barrier-
Additionally, SBM Offshore said another highlight of the ? uid hydraulic power unit with associated spares as well as
Turritella FPSO is its ability to readjust each mooring line’s installation and maintenance tools.
tension without the need to install any device on the FPSO. Shell indicated multiphase sea? oor pumping is planned for “It pioneers the use of an in-line mooring connector (ILMC), a later phase to pump oil and gas from the seabed to the FPSO, which gives direct access to the mooring line for re-tension potentially increasing recoverable volumes and production purposes. This feature allows more ? exibility when the need rates. Shell estimates peak production could achieve approxi- arises to adjust the tension of mooring lines, even during the mately 50,000 boe/d.
early phase of the system installation,” according to the com-
The FPSO pany’s factsheet.
While Stones is the ? rst project in the Gulf of Mexico to uti-
The development lize a FPSO for Shell, it is not their ? rst FPSO project overall.
Shell reached ? nal investment decision on the project in May Shell has 11 other FPSOs globally including the Bonga FPSO, 2013. Stones will be a phased development, with the ? rst 120km offshore Nigeria, in the Gulf of Guinea. Bonga came oedigital.com September 2016 | OE 23 022_OE0916_ Feature1_Audrey.indd 23 8/24/16 12:54 PM