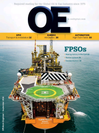
Page 38: of Offshore Engineer Magazine (Sep/Oct 2016)
Read this page in Pdf, Flash or Html5 edition of Sep/Oct 2016 Offshore Engineer Magazine
Seeing the
SUBSEA (electric) light
The sgard subsea gas compression system, Å complete with eActuators and electric process control valves. Image from Statoil. systems, Statoil, at UTC earlier this year.
By the 1990s, work on electric actuators (eActuators) started, with
Statoil using them in 2001, Eidesen says. On the Åsgard subsea gas compression project, the world’s ? rst subsea gas compressor, there are some 79 eActuators, Eidesen says, and worldwide running time of eActuators is above 8 million hours.
Achieving a full electric
Xmas tree took longer, however. In 2003, BP, work- ing with Cameron, developed the ? rst all-electric subsea control system for all-electric a six-month offshore ? eld trial at the subsea tree, and Magnus ? eld, in the UK North Sea, in
Halliburton has quali? ed an electric 185m water depth. An “electric tree” – a downhole safety valve (eDHSV). set of valves and a choke on a skid – was
While
The will is also there. Statoil wants to deployed, not connected to a well, but achieve its own all-electric tree within pressurized from the surface and con-
French oil ? ve years, says the operator’s leader of nected to the Magnus facility for power major Total has subsea technology within the research and communications. However, BP demonstrated the and technology division, at this year’s didn’t take it much further.
It wasn’t until 2008 that the ? rst
Underwater Technology Conference ? rst all-electric Xmas all-electric Xmas tree system, with a (UTC) in Bergen. tree, Norway’s Statoil hydraulic downhole safety valve, was
Operators are keen on an all-electric deployed on two wells, in the Dutch subsea concept because it could remove is eager to do the sector. This summer, a fully all-electric the need to install hydraulic conduits, same. Elaine Maslin system, including eDHSV was deployed reducing cost. Yet, the path to the all- on a third well at the same site (see pages electric subsea tree has been a long one. examines the subsea 38-39). With electrical process control all-electric initiative.
A long electric road valves now proved on Statoil’s Åsgard
The ? rst subsea well was in installed project offshore Norway, a full subsea in 1961, in 17m water depth in the US system, quali? ed to 3000m water depth,
Gulf of Mexico by Shell. It was direct is close at hand, says Frederic Garnaud, hydraulic drive. In the 1970s, electric- deep offshore research and development ith cost ef? ciency and sim- hydraulic systems were developed, to program manager at France’s Total.
pli? cation high on the subsea enable longer distances for control than
W Why electric? agenda, all-electric subsea hydraulics could cope with. facilities are coming back under close The Norwegian Continental Shelf had Christopher Curran – ex-BP, and now scrutiny. its ? rst multiplex electric hydraulic con- working as a contractor for several
All the parts are in place. Subsea trol system in 1986, on Statoil’s Gullfaks companies including Edinburgh-based actuators have become established satellites, says Bjørgulf Haukelidsæter wireless subsea instrumentation and tools, Total has demonstrated a full, Eidesen, leader subsea technology and control and communications ? rm WFS,
September 2016 | OE oedigital.com 40 040_OE0916_Subsea1a_All electric_jl1.indd 40 8/24/16 1:04 PM