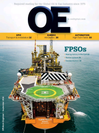
Page 39: of Offshore Engineer Magazine (Sep/Oct 2016)
Read this page in Pdf, Flash or Html5 edition of Sep/Oct 2016 Offshore Engineer Magazine
and consultancy Endeavor Management
SUBSEA – based out of Houston, was involved in the Magnus trial. He says there are a number of bene? ts to going all-electric. “You don’t have to keep ? lling the system with hydraulic ? uid,” he says.
About a gallon of hydraulic ? uid is consumed for every valve operation, points out Bjørn Søgård, segment direc- tor, business development, subsea and ? oaters, DNV GL.“You don’t have people standing around high pressure systems, especially when we’re going to 15,000psi and higher,” Curran continues. “You get an awful lot more data out of the system.
You get more knowledge about the health of the system. You can get some real indication if you’re having issues with a valve, actuator, from scale, wax- ing etc. You get very little information from a hydraulic actuator. And there is potential for savings on the umbilical side. Telecommunications cables are a
A hyperbaric test of Aker Solutions’ subsea rotary electric actuator, simulating fraction of the cost of an umbilical.” 4000m water depth.
Photo from Aker Solutions.
The time it takes to operate a valve is also shorter with electric, Søgård adds, spring failsafe hydraulically operated levels do we need? We don’t know that. due to the time it takes to get back to a valves are used, something the industry No one has agreed a common design so steady state after each operation, with no is comfortable with. Hydraulic pressure we end up with tailor made solutions.” phase lag. Removing the hydraulic ele- holds the spring back, if the hydraulic
Fast forward ments, and even the spring failsafe, replac- fails, the spring closes the valve. ing it with a battery, would also reduce the
Going all-electric means either using Still, the industry is moving forward, size and, therefore, cost of subsea trees, a spring-based failsafe (API required), partly driven by cost reduction, but also as well as the cost to install them, which with a local electronic circuit, or a to help it move into deeper waters and means smaller vessels could be used. clutch solution, so that the open posi- to achieve longer step outs, as part of a tion is maintained using only a small wider all-electric system.
Right timing amount of power, and use a battery as In 2014, even before oil prices plum-
So, why has it taken so long and why the the failsafe option. Total’s K5F-3 is using meted, cost reduction was high on the fuss now? Statoil assessed all-electric a spring failsafe, without hydraulics – agenda for subsea projects, not least in in 2009 for the Tyrihans ? eld, but it more details were not available. Norway. Operators are looking at how to was later canceled. At that time, Statoil Søgård says that while an electric- simplify subsea systems, reducing the found costs were too high, Eidesen says. operated failsafe is not hard to achieve, number of ? owlines, umbilicals, con- “A problem has been that everyone technically – “Xmas trees are simple nectors, etc. All-electric could help. says electric and water do not mix, ‘it’s compared to process equipment” – the Indeed, in 2015, Norway’s OG21 a bad idea.’ If you look at an electric ac- simplicity and industry comfort with group published a report on subsea cost tuator and compare it to hydraulic, you hydraulically actuated Xmas trees reduction. It said that in order to reduce could say it’s too complicated,” Curran means a change in philosophy is needed subsea costs by 50%, an important tech- adds. “But, then, if you look at the whole to move to something else, not least be- nology step was achieving all-electric. system – with a hydraulic power unit cause a well barrier is being dealt with. In addition to achieving an all-electric on the topside, etc. – in those days there “We are in a way reluctant to put on subsea tree within ? ve years, Statoil is was at least parity between the two something delicately engineered to take also working towards a local hydraulic systems in terms of reliability.” care of this safety function,” Søgård power unit subsea – due to be quali? ed
Another reason could be that the says. Statoil’s Eidesen adds that the this year – to power the 7in downhole production control system is only about Norwegian oil major is going to evalu- safety valve, but ultimately, the ? rm 2-5% of the total system cost, Curran ate both options – a spring and a battery wants to see a 7in eDHSV developed.
says. Saving money there doesn’t seem failsafe solution. Furthermore, “Being able to lay a like it would make a big impact in the A subtler problem, as all-electric is power and communications cable, not overall cost, so it wouldn’t seem worth adopted, could be that the industry falls complex umbilicals, will save cost, the risk. into the trap of each vendor producing especially for long distance tiebacks,”
There is also concern around the its own type of electric tree, before there Curran says. failsafe – the function that maintains are standards, Søgård says. “There is a Statoil has done just this on the Johan the tree as a barrier to the reservoir, lack of standards. Shall we use DC or Castberg development offshore Norway.
Søgård says. At the moment, mechanical AC? We don’t know that. What voltage It is planning to use a DC and ? ber-optic oedigital.com September 2016 | OE 41 040_OE0916_Subsea1a_All electric_jl1.indd 41 8/24/16 1:06 PM