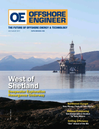
Page 30: of Offshore Engineer Magazine (Jul/Aug 2019)
Subsea Processing
Read this page in Pdf, Flash or Html5 edition of Jul/Aug 2019 Offshore Engineer Magazine
FEATURE Topsides of Mexico and mixing that together,” he says. “It’s a big ele- and a 228-metric-ton module on the topsides.
ment in how we were able to reduce costs on the project.” “We tried to maximize the things we could do here at
As originally designed, Peregrino Phase 2 was projected Kiewit,” Haldorsen says. to cost $4.3 billion. But by applying strategies that included The topsides itself is 95 meters long, 57 meters wide, and 49 embracing the “Gulf of Mexico way” of executing projects, meters high. The main support frame for the WHP-C topsides including standardization of equipment, using tie-in concepts weighs 10,500 metric tons while the completed topsides gross to existing Peregrino facilities and subsea solutions causing operating weight is 23,000 metric tons. fewer topside modi? cations, and ef? cient drilling methods It is always critical to keep the weight of the topsides from and new contracts for drilling and management services in creeping up, he notes.
Brazil, the team was able to shear $1.3 billion off the project, “A benchmark of a lot of projects is you see weight going resulting in project sanction in February 2016. up and up. You have to buy more steel and fabricate that steel
Haldorsen says the ability to “adapt to the yard” and un- and move that steel,” he says. derstand the local work processes is necessary for succeeding Controlling the weight was one method of keeping costs with a big project. “Whether we go east or west, that’s what down, he adds.
we need to know. What is the Gulf of Mexico way of doing “We are in the last phase of our schedule, and the good news things? And that way you can succeed,” he says. is we are on track to milestones and the budget,” he says, not-
One sign of success is weight control, and by avoiding ing a focus on health, safety and environment (HSE) has been weight increases, the project was able to move offshore lifts a cornerstone of the development. As of late June, the job in onshore to minimize the number of offshore lifts required, the Kiewit had tallied 3.5 million manhours with no lost time in- company said. cidents. Another part of the focus has remained on using new “When we reduce the offshore scope, we reduce the off- as well as proven technology and adapting digital solutions to shore work, as well as the potential for things that could be an keep operational and maintenance costs down once the unit is
HSE trigger,” Haldorsen says. operational, he says. As such, the designers looked at how to
As a result, two of the drilling modules will be lifted onto reduce the number of people required for operations without the topsides onshore at the Kiewit facility, rather than as off- compromising HSE.
shore lifts. Onshore lifts will place a 377-metric-ton module Part of keeping maintenance costs down includes high-
Peregrino Phase 2 opens up the southwest extension of the
Peregrino field and makes it possible to recover an additional 273 million barrels. The WHP-C platform, which will drill a series of production and injection wells, will send the production stream to the
Peregrino FPSO and will receive treated water for injection.
Source: Equinor 30 OFFSHORE ENGINEER OEDIGITAL.COM