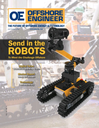
Page 16: of Offshore Engineer Magazine (Jul/Aug 2020)
Read this page in Pdf, Flash or Html5 edition of Jul/Aug 2020 Offshore Engineer Magazine
MAINTENANCE UPDATE Bearings
BEARING SURFACE DAMAGE:
SHOULD ALARM BELLS BE RINGING?
SMB233 - Designing for the ofshore environment
By Chris Johnson, Managing Director, SMB Bearings efect classi?cation is a crucial step in determin- primary forms of this pesky enemy, bearing corrosion usually ing if goods should pass or fail a quality control falls into two broad categories — moisture corrosion or fric- inspection. Minor defects usually don’t affect the tional corrosion.
Dfunction or form of the item, whereas major de- Moisture corrosion is particularly commonplace in offshore fects could adversely affect the function, operational perfor- drilling environments and worryingly, can appear on any mance, or aesthetics. But, how do you determine when aes- component of the bearing. For example, if bearings are often thetic surface damage needs action? Here, Chris Johnson, exposed to moisture or mild alkalinity due to their contact managing director of bearing specialist SMB Bearings, ex- with seawater, this could create an alarming oxide layer as a plains why not all bearing surface damage should cause alarm result of a chemical reaction with the metal surface. Mild cor- and future headaches for offshore oil and gas plant managers. rosion may result in light surface stains, but in severe cases, it can lead to etching on the surface of the bearing, resulting in
Bearing surface distress can take many forms and can result ?akes of rusted material entering the raceway. in problematic symptoms such as excessive heat, increased In these instances, corrosion can graduate from an aesthetic noise levels, increased vibration, or excessive shaft movement. inconvenience to a very real drain on a business’ bottom line.
However, not all external bearing ?aws point to compromised According to the IMPACT study conducted by NACE Inter- internal machine performance. national, the world’s leading corrosion control organization,
One such form of bearing surface damage is corrosion. This it has been estimated that 15-35 percent of annual corro- is a naturally occurring phenomenon that offshore oil and gas sion could have been saved if optimum corrosion manage- plant managers must commonly confront. While there are ten ment practices were followed. This equates to savings between 16 OFFSHORE ENGINEER OEDIGITAL.COM