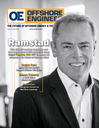
Page 43: of Offshore Engineer Magazine (Mar/Apr 2021)
Offshore Wind Outlook
Read this page in Pdf, Flash or Html5 edition of Mar/Apr 2021 Offshore Engineer Magazine
TECH FILE SUBSEA SIM AND TESTING valve or system, consideration must be taken into account for with the presence of seawater, especially when stagnant, can the potential of material galling from low-viscosity fuids. Ad- corrode and compromise the structure of the valve compo- ditionally, phenomena such as corrosion, cavitation and high- nent. It is imperative to design valve components in subsea pressure surges all contribute to the valve design decisions. systems with high-corrosion and pitting resistance to avoid • MAINTENANCE: Because this type of subsea equipment stress-cracking issues. As the industry changes, design engi- can operate miles below the surface of the ocean, equipment neers should stay current with industry standards, material is not easily maintained. Therefore, it must be designed for properties and manufacturing methods in order to make the maximum service life. Incorporating design features that act as best component selection decisions.
a layer of defense against failure, such as a “last-chance” flter • VENT-TO-SEA: Vent-to-sea hydraulic systems require leak- built into valves to help prevent contamination, are important. tight internal sealing to contain the fxed volume of stored
Additionally, for the subsea oil and gas industry, users are more fuid in subsea accumulators. This means that typical hydrau- interested in repairing components as opposed to replacing lic designs must be adapted to reduce or eliminate the inter- them, so serviceability of components must be considered. nal leakage that is acceptable practice in closed-loop hydraulic • SHOCK & VIBRATION: The high-pressure and high-fow systems. The systems must also have leak-tight external con- systems in subsea oil and gas applications create signifcantly nections; this is required of all hydraulic systems, but especial- more shock and vibration than what is seen in standard hydrau- ly so of those operating subsea. To accomplish this, engineers lic systems, which are usually high-pressure and low-fow or low- need to develop, or work with a developer of, resilient sealing pressure and high-fow. Shock and vibration in these systems can technologies for both hard- and soft-seated designs. For exter- lead to premature failures including leaks, sticking, or in extreme nal piping and connectors, subsea validated technologies like cases loss of function. System designers need to manage the hy- Parker’s Dual Seal/Seal-Sub fanges and Phastite non-welded draulic fow paths to minimize shock in the system. One way to piping system are best used for safe and reliable connections minimize this shock is to incorporate proportional pressure and between valves, accumulators, and cylinders and are preferred fow control valves that will better manage the release of energy. alternatives to unreliable tapered threads, pipe fanges, and • CORROSION: The harsh operating conditions, coupled socket welded interconnect piping.
Source: Parker Hannifan march/April 2021 OFFSHORE ENGINEER 43