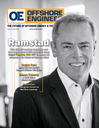
Page 45: of Offshore Engineer Magazine (Mar/Apr 2021)
Offshore Wind Outlook
Read this page in Pdf, Flash or Html5 edition of Mar/Apr 2021 Offshore Engineer Magazine
TECH FILE SUBSEA SIM AND TESTING to have simulation subject matter experts develop analytical level of product reliability. Coupling both 1D and 3D simula- models and further validate them with real-world tests. Vari- tions for high-fdelity modeling, also called co-simulation, is ous types of simulations across multiple domains of physics a best practice that design engineering teams should incorpo- with varying complexities can be performed, including: rate. When simulating for hydraulic systems, ensure that the • 1D – Lo w- and high-fdelity component and system entire hydraulic circuit is modeled rather than using simpli- simulation fed models from combined parameters in order to achieve • 2D/3D – Transient dynamic CFD simulations high-fdelity results from simulation.
• 2D/3D – Fluid structure interaction (multi-phase phys- Additionally, simulation can aid in expanding further into ics: FEA and CFD) market segments by optimizing and simplifying designs for • 2D/3D – Multi-phase fuid fow and water hammer CFD better performance, reducing the number of parts, lowering • 3D – N on-linear implicit and explicit FEA costs and more. All of this can increase product reliability and
Extensive analysis with an intent of validation and correla- customer confdence while reducing time to market.
tion of the analytical models with test and feld data led to the development of new simulation techniques and methods that Application Testing Validates Simulation Outcomes
Parker has used across a wide variety of projects. Additionally, In the testing environment, industry standards require direct engagement with both internal and external simulation supplementary information that outlines exactly how a spe- software vendors, material scientists and manufacturing ex- cifc test should be run. System designers should work with perts was critical to develop intellectual property and a strong OEMs, system integrators and the end user to fully defne simulation knowledge base that has been progressively devel- testing requirements. Once requirements are in place, teams oped and updated over the years. The simulation validation can construct research and development rigs that will closely and test correlation process used to create better and more ac- mimic the application conditions. At this stage, engineers will curate predictions involved in-depth experiment designs and want to minimize fuid connector changes such as changes to stochastic/sensitivity studies for variables including element line sizes, fow directions or other functions that can serve to types, turbulence models and contact models. artifcially remove energy from a system, creating an easier-
The ability to accurately model complex physical phenom- than-intended test. They will also want to deploy the maxi- ena like multi-phase fow problems to examine microscopic mum energy in the testing environment by using higher fows wear and further validate these results with tests encour- and pressures than the application will actually require.
aged qualitative testing during the research and development It is important to incorporate both common and unique phase. This synergy between simulation and test enables a hydraulic testing in development processes. By creating cus- group working in a thriving simulation ecosystem to model tom tests, teams can make sure to leave no stone unturned in innovative concepts and build intellectual property. the design process. It is also critical to conduct necessary test-
With the right hardware, it is possible to conduct the com- ing for type approvals from certifying bodies. Depending on plex analyses required to design hydraulic valves. However, the specifc application, these may include burst, fre, rated fa- if this is required of all users, this can become a large fnan- tigue pressure, water hammer or cyclic fatigue, corrosion and cial burden. By focusing on simplifying some of these tools, bend testing. Validation through physical testing is the key both design engineers and non-expert analysts will be able to to building confdence in simulation-based predictive models. use these tools to model even the most complicated interac- It has been said that “all the easy oil has already been got- tions on their CAD terminals. This enables scalability without ten.” The offshore deep-water environment is challenging, compromising on accuracy. and the technology requirements are only becoming more de-
Building a simulation ecosystem within an organization manding as exploration warrants deeper water depths beyond will help to create a culture where simulation is trusted to 12,000 feet. both help new ideas fail fast and fail early, as well as assist These more demanding subsea atmospheres require higher with tuning or smaller adjustments near the end of a develop- system pressures and increased design fdelity. In response, ment cycle. Prototyping new and truly novel solutions is sig- Parker is creating new models to intelligently and proactively nifcantly less risky in an ecosystem where there is a high level advance the functionality of its products to help avoid un- of confdence in designs proven by simulation. Integration of planned downtime and bring better processes and effciency quality tools like Design for Six Sigma can add an even deeper to the market.
march/April 2021 OFFSHORE ENGINEER 45