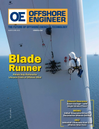
Page 29: of Offshore Engineer Magazine (Mar/Apr 2022)
Read this page in Pdf, Flash or Html5 edition of Mar/Apr 2022 Offshore Engineer Magazine
wind tower inspection. It also has application in shipping, The platform will use a distributed approach to localiza- to perform UWILD activities, as well as oil and gas, where tion, says Corsar, which means that it uses different sourc- the company has been working with Oceaneering on risers es of information, such as existing knowledge of the asset, and caissons, says Corsar. e.g. bolt spacing.
“In a relatively fresh development we’re starting to team
Robot bolt tensioning up with another company looking at BVLOS comms via
Using the same platform, Innvotek is now also working satellite where hopefully all the robot control can be done on another robot designed to perform bolt inspection and from the shore, within the next 12 months, using low la- tensioning. This vehicle will have “a lot more features and tency satellite communications.” a lot more intelligence in it in terms of understanding its Innvotek is also part behind the Fire? y Inspect project, environment and capability in terms of tooling. Routine with partner Mapair. The project involves a drone that inspection and cleaning, physical interaction with the asset uses infrared technology (a 1,000W heat lamp) and AI to to torque up a bolt.” The project is about nine months in, inspect for hidden imperfections composite structures (a and then computer vision to identify bolts and then orient technology initially developed for inspecting plane wings). and align tooling and then do 99% of the torqueing itself; A trial system, complete with an OptiTrack motion cam- “it will just need a go, no-go command”. era technology for navigation, was demonstrated at ORE
Catapult’s Blyth test facility earlier this year.
BladeBUG
Another robot, BladeBUG, is looking at turbine blade inspection and surface preparation, as part of repairs.
Company founder Chris Cieslak came up with the idea in 2014, while working as a blade turbine engineer. In 2017, he decided to go full time on the idea, supported by ORE
Catapult. It’s a six-legged robot, with each leg having its own vacuum cup system to help it creep across and work on blade surfaces. It’s tethered and human operated via a semi-autonomous motion system – the operator uses a joy- stick to tell it to move forward, back, left or right, and the robot scans the surface to plan how to move its feet. “It’s designed to be taken offshore so it’s small, compact and lightweight (600mm-wide and -long and weighing 20kg). It’s about trying to change the mindset of wind. It’s very reactive, currently. They wait for damage to get severe enough to send out rope access crew. During that period the blade is becoming more inef? cient. [With BladeBUG you can] start to see a problem and treat it early, potentially preventing cases where you could get a catastrophic defect.”
A common issue is leading edge erosion, which happens when rain hits the blade as it travels at up to 200mph, mak- ing its smooth pro? le rough and pitted. This effect then ac- celerates, says Cieslak. As is the case for a chip in a car wind- screen, early treatment can prevent a catastrophic failure.
A lot of the development work has been on the blade walking capability, which was proven on ORE Catapult’s 7MW trials turbine at Blyth. It’s also been developing its capabilities, which include testing the lightning protection system on blades and UT inspection, to see any issues un- march/april 2022 OFFSHORE ENGINEER 29