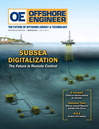
Page 58: of Offshore Engineer Magazine (Sep/Oct 2024)
Read this page in Pdf, Flash or Html5 edition of Sep/Oct 2024 Offshore Engineer Magazine
TECH TALK VALVE REPLACEMENT tem, allowing for the isolation of sections for repairs and
Case Study 1: replacements. In this case, the AOGV enabled the ?ow meter replacement on the butane pipeline while minimiz-
Replacing a Flow Meter on a ing gas freeing and keeping the main process operational.
Live Butane Pipeline
An 18-inch ASME Class 300 AOGV was designed, en- gineered, and manufactured for the application. Working closely with the facility owner, we attended a HAZID on the site and hosted a Factory Acceptance Testing at our
Stavanger workshop.
Identifying Asbestos within the gasket in question,
Izomax engaged with specialist handlers in advance, while developing a brushing tool to safely remove any remaining debris. The performance of the AOGV was veri?ed for high pressure services using ?nite element analysis and by pres- sure testing to 1.43 times design pressure (as per the EU
Pressure Equipment Directive (PED) (2014/68/EU) and
EN 13445 – Un?red Pressure Vessels prior to deployment).
A team of ?ve Izomax AOGV specialists carried out this onshore operation, lifting the AOGV into place via a mo- bile crane, before scaffolding and rigging was used to as- semble and deploy the system. Providing positive isolation, the AOGV mechanical isolation tool inserted an isolation spade between a ?ange pair and a built-in isolation valve, enabling depressurisation and gas-freeing of a very short section of the pipeline. The isolation allowed for removal and replacement of the leaking ?ow meter, whilst keeping the liquid butane inventory within the pipeline.
Timely completion was essential, as the terminal’s bu- tane tanks had only three weeks of production capac-
Photo courtesy Izomax ity. Izomax completed the operation in two weeks. The
Working with the Izomax AOGV to replace a leaking flow
AOGV’s ability to isolate the pipeline provided the only meter on a 18-inch butane pipeline described in case study 1. effective solution. The operation was executed without any n 18-inch class 300 butane pipeline, spanning 11 km health, safety, or environmental incidents, and no non-
A and operating at 12 bar (175 psi), had a leaking ?ow me- productive time was incurred.
ter that needed to be isolated for replacement during a brief,
No hot work was required, signi?cantly reducing three-week window. Pipeline design entailed that it could not time, cost, and health, safety, security, and environmen- be fully drained and re?lled, making conventional solutions tal (HSSE) risks. The asbestos in the existing gasket was impractical. Located in a residential area, the asset owner safely handled and disposed of through an approved de- sought to avoid the risks and costs associated with a complete contamination process on-site. The integrity of the system pipeline replacement. There were no suitable isolation points was maintained throughout, and the plant was restored to near the defunct meter, limiting intervention options. Several its original operating condition without complications.
alternative solutions had been deployed to attempt to solve
By avoiding a production shutdown, the Izomax AOGV the external leak, without success. Further complicating mat- system saved the operator an estimated $15 million USD. ters, asbestos was discovered in the gasket, requiring special-
This direct ?nancial saving, combined with the mitigation ized handling, decontamination, and disposal procedures.
of operational risks, made the AOGV technology the key
Izomax’s patented AOGV provided a mechanical isola- factor in the success of the project. Without it, a much tion solution without hot work. The tool can insert and costlier and riskier alternative would have been necessary.
retract a blind spade between ?anges on a pressurized sys- 58 OFFSHORE ENGINEER OEDIGITAL.COM