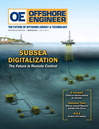
Page 60: of Offshore Engineer Magazine (Sep/Oct 2024)
Read this page in Pdf, Flash or Html5 edition of Sep/Oct 2024 Offshore Engineer Magazine
TECH TALK VALVE REPLACEMENT line, while the main process is kept in continuous operation.
Case Study 2:
A 36-inch ASME class 150 AOGV system, the largest developed to date, was designed, engineered, and manufac-
Replacing a Stuck Butterfly Valve tured for the valve replacement operation on the live ?are at a Supermajor LNG Plant system. The design incorporated geometrical constraints from the site, adhered to the Pressure Equipment Direc- tive and EN 13445 standards and was veri?ed through third-party FEM/FEA analysis. DNV assessed the tool's conformity, including design review, material evaluation, and production oversight. Pipe ?exibility was also analysed to ensure the system met piping design codes.
Detailed planning was conducted in collaboration with the facility owner, including site preparations and opera- tions. A HAZID was performed, and the customer attend- ed a Factory Acceptance Test at Izomax’s facility in Stavan- ger. Testing of the AOGV tool at cryogenic temperatures (-196°C) was completed, and the operation was rehearsed on a mock-up rig before shipment to the site.
During the operation, scaffolding and rigging support were provided by the site owner, and coordination among personnel in the con?ned space was critical. The Izomax
AOGV system was installed and suspended to prevent ad-
Photo courtesy Izomax
Replacing a defunct butterfly valve on the 36-inch flare flare ditional load on the pipework. After leak testing, the ?ang- line of one of the world's largest LNG facilities, as described es were separated for approximately 30 mm, and a blind in case study 2. spade was inserted for positive isolation at the upstream ?ange. The faulty valve was safely removed and replaced, t one of the world’s largest LNG facilities, a butter?y following agreed procedures. and the system returned to
A valve on a 36-inch class 150 ?are line operating had normal operation. The AOGV mechanical isolation sys- been stuck in a closed position for an extended period. tem was reinitiated, the blind spade removed, and the sys-
The stuck valve prevented the backup ?are system from tem brought back to normal operation. The main ?are was being used, thus limiting the options available to undergo operational throughout the entire operation.
planned maintenance without shutting down the entire
The entire operation was completed without any HSSE plant. The working temperature of the line could range incidents or downtime, to the client’s satisfaction. The from ambient to cryogenic in the event of a sudden slugs AOGV system solved a long-term issue that other tech- of liquids, and the faulty valve needed to be replaced. Solu- nologies could not address due to unacceptable risk levels. tions were required to mitigate HSSE risk associated with Despite logistical challenges due to worksite location, the the valve replacement, as there were no suitable built-in tool was delivered and operated on schedule.
isolation points close to the stuck valve. The plant opera-
The plant's system integrity was maintained throughout tor had evaluated alternatives, concluding that few, if any, the process, with the ?are returned to its original condition robust or cost-effective solutions were available.
after the AOGV operation. The LNG plant was running
The Izomax AOGV mechanical isolation tool which can full speed through the complete operation, no interference set and retract a blind spade in a pair of ?anges on a pres- to the delivery of the LNG.
surised process system, e.g. a ?are system, without hot work.
This project highlighted the ef?ciency, safety, and cost-
The blind spade or a combination of several spades in dif- effectiveness of the AOGV system. The ability to isolate ferent locations can facilitate the replacement of valves and equipment without disrupting operations makes it a valu- pumps. The AOGV can also be used to take a vessel out of a able tool for similar industrial applications, where tradi- closed loop temporarily for safe entry and bringing it back on- tional methods pose higher risks.
60 OFFSHORE ENGINEER OEDIGITAL.COM