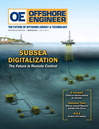
Page 61: of Offshore Engineer Magazine (Sep/Oct 2024)
Read this page in Pdf, Flash or Html5 edition of Sep/Oct 2024 Offshore Engineer Magazine
Building a Pressure Chamber Around the Flange basis for designing the hardware to be produced for the
In essence, the principle of the AOGV is to build an speci?c purpose. entire pressure chamber around the ?ange to contain the The main principle of the AOGV is the same for all pressurized contents. The pressure chamber unit incorpo- pipe dimensions, from 2-inch pipes up to our largest rates bolts that can compress the ?ange, relieving force on AOGVs to date, the 36-inch pipes described in the second the original bolts so they can be loosened. A separation of case study. But of course, complexity increases with the a couple of centimetres then allows a mechanical blocking larger pipe diameters as the weight and size of the AOGVs device like a blind spade or a spectacle blind to be inserted involved create their own logistical and HSE challenges. before re-tightening the ?ange. The same principle allows The second-generation AOGV we use today has improved for a wafer butter?y valve to be replaced, as the valve is from the ?rst-generation version in that we have added situated between pipe ?anges. hydraulic compression of the ?ange to the unit, replacing
To isolate a section of pipe, blind spades may need to the bolt compression we ?rst used.
be inserted at several points, leaving the section mechani- Izomax is in the maintenance and repair business, and cally isolated so work can be done. Achieving smart inter- for operators facing huge and complex maintenance and re- ventions on a working process plant, requires that there pair challenges, what matters most is to ?nd the least costly are redundancy sections that can take over the operational option. The alternatives for operators are, in many cases, workload. The inherent capabilities of the AOGV tech- to shut down installations completely and bear the mas- nology uncovers at lot more of micro redundancy with its sive cost of revenue loss during downtime. Operators easily ability to insert positive isolation in any ?ange pair. see the bene?ts of AOGV, frequently commenting that the
Pressure is de?nitely one of the main challenges, but so technology has revolutionized their maintenance options.
are the dimensions of the piping involved and the com- Offering the alternative to isolate smaller areas for re- plex nature of a processing plant. Plants and any sort of quired maintenance, and execute planned, predictive piping installations can be messy places, with close prox- maintenance on crucial components, the AOGV entails imity to other piping, constraints such as walls and a gen- a cost-effective option to shutdowns. In cases where there eral lack of space. That is why the majority of AOGVs are parallel process segments for redundancy backups, are designed as bespoke units. A close inspection of the AOGV operations on one segment will not impact the worksite, and even 3D scans in some instances, are the overall operation of the installation. september/october 2024 OFFSHORE ENGINEER 61