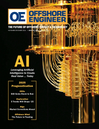
Page 29: of Offshore Engineer Magazine (Nov/Dec 2024)
Read this page in Pdf, Flash or Html5 edition of Nov/Dec 2024 Offshore Engineer Magazine
MARKETS FLOATING WIND technical drivers, summarizes the fndings of the latest re- construction yards on heavy lift vessels. Concrete concepts search, presents a deep dive into each of the major foating are generally more suited to local manufacture and assem- wind markets and translates the activity forecast into a ves- bly. Depending on the concept selected, each foater for sel supply and demand balance forecast. current generation turbines could weigh from below 5,000 tonnes to 20,0000 tonnes. A commercial scale project will
THE MARKET IS GROWING – BUT POSSIBLY require ~30-35 of these foaters per year to meet installation
NOT AS QUICKLY AS SOME BELIEVE requirements of one full installation spread.
As we have mentioned previously, foating wind is an • Turbine installation is generally expected to take emerging technology. Concepts are still be demonstrated place at the assembly port. Next generation turbines with in single turbine and small pilot arrays. The frst commer- larger diameters drive the hub height where a crane needs to cial scale arrays (±500 MW) with offshore construction lift weights of 750-1,050 tonnes to over 180 meters assum- activity within this decade are being planned for such mar- ing the currently available large turbines. A key variable to kets as South Korea and the UK. monitor is the development by Chinese developers of tur-
From around ~305 MW installed at the end of 2024 bines as large as 25 MW with rotor diameters of ~300-310 to ~6 GW (2030) and ~48 GW (2035). Market growth meters. Suitable crane supply is limited today and with po- anchored by Europe in the frst half of the next decade. tential increases in rotor diameters will become even more
Through this decade, we anticipate that South Korea limited. Once assembled, several turbines will likely be wet will be the largest foating market, but the frst half of the stored before being towed offshore for hook-up. Due to in- next decade is likely to be dominated by activity in Europe, stallation season weather windows, this period could last with the UK, France, Italy, Portugal forecast to be the most 4-6 months. The implication is that a suffcient supply of active (but not only) foating wind markets. The U.S. en- suitable large, sheltered harbor facilities is required.
ters the foating wind stage during the forecast period with • A station keeping system is required for the foat- both pilot and commercial scale developments on the West ing turbines. There are many different solutions available
Coast and pilot arrays on the East Coast. depending on the specifc site conditions and foater design, but suction anchors, drag embedment anchors and driven
HOW DO YOU BUILD A FLOATING WIND FARM?
piles are likely to feature in most projects in the short- to
At a high level, building a foating wind farm can seem mid-term. Again, depending on a number of variables, to be a simple exercise, as shown in the graphic. anchors can be shared by mooring lines or each mooring
However, the uncertainty over what we will be installed, line can feature an anchor. The base case is for each foater volumes of components to be handled and their sheer to generally require three mooring lines, either in a 3x1 (3 physical size present many challenges to foating wind de- lines per foater) confguration, a 3x2 layout or even 3x3. velopers. Let’s look at the differences that sets the build- The uncertainty over the technical solutions drives us to de- ing of a foating wind project apart from the established velop our three base scenarios (mutualized suction anchors, bottom-fxed segment to understand these challenges of drag embedment anchors and taut mooring with suction technical uncertainty, volumes and sizes of components. anchors) to present an order of magnitude of the volumes • It star ts with the foater, for which there are more of components, the demand for vessels and to highlight than 100 concepts being developed globally that are broad- the impacts and major differences in the various technical ly grouped in semi-submersibles, barges, spars and TLPs. choices. It is likely, at least in the short-to-mid-term, that
These concepts can be built from steel (rolled stiffened mooring systems will feature sections of large chain (~130- plate, fat panel construction and heavy-walled tubular, 1800mm) and sections of large fber rope (±300mm). etc.) or concrete (slip formed, pre-cast, with reinforcement, • Complete assemblies will be towed offshore by a with post tensioning tendons, etc.). Some concepts feature spread of tugs including lead, support, and security tugs steel plate construction familiar to shipbuilders while oth- and then hooked up to the pre-laid moorings. Tensioning of ers rely on large diameter steel pipes produced at offshore the mooring system will generally be required, more often wind monopile and tower manufacturing plants. Steel con- than not from the vessel rather than the foater. It should be cepts can be manufactured in sub-assemblies and shipped noted that the impact of larger turbines referenced earlier to assembly yards or can be shipped as complete units from will likely be larger foaters and more robust (larger in num- november/december 2024 OFFSHORE ENGINEER 29