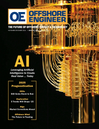
Page 30: of Offshore Engineer Magazine (Nov/Dec 2024)
Read this page in Pdf, Flash or Html5 edition of Nov/Dec 2024 Offshore Engineer Magazine
MARKETS FLOATING WIND ber and/or size) moorings, which of course can increase the in the short-to-mid-term. More than 14 million meters of ar- technical requirements for towing and hook-up vessels. ray cables are also forecast to be installed in the period.
• Array cables can be pre-laid and wet-stored with the The characteristics of the components drive the need moorings or installed when the foaters are hooked-up. A key for large anchor handlers and subsea vessels. In our report, difference in foating wind array cable systems to those found the detailed technical analysis takes the reader through the on bottom-fxed projects is that the subsea cables are fexible or drivers to understand the constraints in terms of capac- dynamic and are suited to deployment by vertical lay systems. ity, capabilities and effciencies of vessels and why the large • Substations can be bottom-fxed, foating or even vessels will be required.
subsea, depending on the specifc project site characteris- The simple conclusion is that there is insuffcient tech- tics. Export cable laying is for the most part the same as nically capable vessel supply to meet forecast demand in seen in bottom fxed wind farms. the next decade.
TURNING THE FORECAST INTO ARE BIG, EXPENSIVE FLOATING WIND
VESSEL DEMAND SPECIFIC VESSELS THE ANSWER?
We have prepared a bottom-up forecast for activity The quick answer is “no”.
through 2035 and have developed demand models for Unless charters agree long-term vessel utilization, there three scenarios: will be likely be several months every year where a foat- • Mutualized catenary mooring lines (very large di- ing wind specifc vessel will be underutilized. Long-term ameter chain and fber rope) connected to suction anchors. charters commitments will be needed to justify investment • Drag embedment anchors, two per foater mooring in high-cost assets. These conditions do not currently exist.
connection, connected to individual catenary mooring lines There is a greater argument for large subsea vessel build- (large diameter steel chain, smaller than that of the mutual- ing, due to the fexibility of the assets to work in both oil & ized and taut mooring case, and a fber rope mid-section). gas and offshore wind (bottom-fxed and foating) space. • A taut mooring system with a smaller footprint, But the high-specifcation anchor handlers required by with predominantly fber rope mooring lines and connect- foating wind projects are a more diffcult investment case. ed to induvial suction anchors. What most foating wind projects will require is generally
The mooring scenarios deliver signifcantly different results technically very different from most oil & gas projects. As of anchor demand (~10,000-30,0000 anchors) and mooring a result, a typical large oil & gas anchor handler will lack lines (~17,000-35,000). We expect to see all three systems one or more of the key technical features to be an effcient used, although the catenary systems are likely to be preferred tool for commercial foating wind projects.
30 OFFSHORE ENGINEER OEDIGITAL.COM