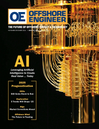
Page 51: of Offshore Engineer Magazine (Nov/Dec 2024)
Read this page in Pdf, Flash or Html5 edition of Nov/Dec 2024 Offshore Engineer Magazine
MAINTENANCE OFFSHORE WIND
GettyImages courtesy Regal Rexnord
The High Stakes of Yaw Brake Repair Revolutionizing Brake Disc Resurfacing
Wind turbines have become bigger, with taller hub The turbine operator was looking to minimize any down- heights and larger rotors. This increase in size creates ad- time associated with disc resurfacing operations. To do so, it ditional challenges for maintenance and repair efforts, es- contacted Svendborg Brakes, a part of Regal Rexnord, and pecially for offshore installations where the turbines can be asked to develop a solution that would address the require- located 1-2 hours away from land. ment of removing the brake systems from the tower. The
The yaw system of the wind turbine generators (WTGs) company was selected due to their comprehensive brake re- has the essential role of orientating the nacelle towards the pair services in wind turbines, which has proven to stream- wind and holding it in position. Performing both yaw stop- line overall maintenance and repair operations by providing ping and holding functions, the brakes are under constant all the services that typically require multiple contractors. use and are required to operate reliably. The condition of the Svendborg Brakes has solutions installed in over 200,000 brake disc surface is key to the brake system’s performance, wind turbines globally, both on and offshore.
it must be smooth and remain free from damage. Over time, Thanks to their extensive expertise in braking systems the surface of the yaw brake will begin to suffer wear and and its suite of components that are manufactured in- small imperfections will appear. These imperfections will af- house, Svendborg Brakes was able to develop an innovative, fect yaw brake performance and ultimately reduce the pro- portable disc resurfacing tool. This tool consists of a milling ductivity of the WTG – eventually leading to a failure, which machine that quickly repairs the disc onsite while minimiz- could cause compound damage to other components. ing the quantity of fne dust produced during the process.
If the WTG were to fail, the repair would require re- James Woods, Senior Project Manager, Engineering & moving the nacelle of the turbine to access the yaw sys- Test at Svendborg Brakes, said, “With only 1 mm thickness tem. This would be very expensive, requiring the use of a of material removed from the disc, the solution we developed crane, additional labor, and increased downtime. Instead was able to exceed our expectations, delivering an end result of replacing the brake disc, operators utilize a resurfacing of extremely high quality. Even more, the process is extreme- process to eliminate the imperfections which is tradition- ly fast, with less than a day required to repair the disc.” ally a time-consuming task. Many operators accept the The groundbreaking tool is extremely compact and light- downtime caused by disc resurfacing as an unwelcome but weight, allowing it to be easily transported to the top of the essential chore. However, when one custodian of several wind turbine. The disc resurfacing tool is mounted using
WTGs off the coasts of Denmark and the UK identifed one of the yaw brake mounting positions. This is an easy to that several of their yaw brakes were damaged, they were install and minimally invasive process. The disc resurfacing eager to fnd a solution that could expedite the process. tool can also be operated manually or automatically, via sin- november/december 2024 OFFSHORE ENGINEER 51