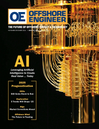
Page 52: of Offshore Engineer Magazine (Nov/Dec 2024)
Read this page in Pdf, Flash or Html5 edition of Nov/Dec 2024 Offshore Engineer Magazine
MAINTENANCE OFFSHORE WIND
DRT Before DRT After gle-axis computer numerical control (CNC) – the latter be- a complete pad exchange within this timeframe.
ing accomplished using the company’s proprietary software. Svendborg Brakes’ experience in wind turbine opera-
It is possible to map the surface of the disc to create a CNC tions and yaw brake systems was crucial to bypass dis- machining profle that the disc resurfacing tool uses to ac- mantled components and allow the WTG to run during curately follow the disc. Since this process does not require the night. As a result, it was possible for the operators to the turbine nacelle to be removed to resurface the yaw brake generate power for at least 12 hours every day, yielding disc, the operator saw three major areas of cost savings: no 50% more uptime than most typical projects of this scope. lifting equipment required to remove the nacelle, no supply After the successful development of a new disc resurfacing vessels needed to complete a replacement project, and no tool and its adoption for the repair of wind turbines off purchasing and installing of a new yaw brake disc. the coasts of Denmark and the UK, Svendborg Brakes has discussed future projects with the WTG operator as well as
Continued Innovation for the Future of Wind other wind turbine owners and operators.
As a full-service provider of braking solutions, Svendborg As the industry continues to see signifcant growth, manu-
Brakes was able to combine additional elements to stream- facturers must navigate increasing logistical complexities and line the entire maintenance process. First, the repair team the need to adapt their operating models to keep up with could utilize an LBS yaw brake lifting tool developed in- market demands and challenges. As turbines continue to house to quickly and easily remove the brake from the disc grow in both size and output, the durability of components as well as reinstall them afterwards. The entire project could is out to the test, with quality issues leading to signifcant op- then be completed in three days, which is incredibly brief erational and fnancial consequences. Regal Rexnord™ pro- compared to “typical” brake pad removal/replacement proj- vides complete solutions for the Wind industry, from design ects. In addition, the specialized teams were able to perform and manufacturing to installation and continuous support.
52 OFFSHORE ENGINEER OEDIGITAL.COM