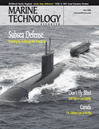
Page 30: of Marine Technology Magazine (May 2008)
Undersea Defense Edition
Read this page in Pdf, Flash or Html5 edition of May 2008 Marine Technology Magazine
30 MTR May 2008 out and the 3-D concept model. The 3-D inertial posi- tioning, as well as the heading, pitch, and roll informa- tion, our output directly from the subseahoused INS to a fiber-optic multiplexer on the ROV and transmitted top- side across the umbilical. From the topside fiber-optic multiplexer, text strings of data from the INS are trans- mitted across an RS-232 port which can be easily read into Hypack and parsed according to the respective data fields. SeaVision also developed a simple representative model of the SeaEye Falcon with the reference point set to match the reference point of the INS. Prior to the mis- sions, SeaVision also developed conceptual models of known large obstructions in the tunnel, particularly a scoop loader (a low-profile front-end loader) and a bobcat skid-steer and a scissor lift. Using this information, the
ROV was to be flown through the virtual space much like a video game, using sonar primarily for obstacle avoidance and tunnel mapping duties. The 2-D and 3-D models could be viewed by the ROV pilot, in real-time, in order to navigate safely from the access shaft to the bulkhead door and back to the access shaft.
ROV Ops in a Flooded Mine
The portion of mine to be investigated, at the 480 m level (480 m below ground surface, or approximately 464 m in depth), had been near completion. As such, it was full of utility lines along the ceiling and sidewalls. During the evacuation that followed the accidental rock fall and subsequent flooding, the miners (all of whom escaped safely) abandoned toolboxes and heavy equipment. The exact location of these items was not known. Access could only be gained from the vertical access Shaft 1, which would require that the SeaEye Falcon DR be lowered within a deployment garage to the level to be investigated.
By integrating the deployment garage into the elevator system, the Falcon and the garage could be lowered to the elevator shaft chamber at the deployment level. The posi- tioning and orientation of the garage required that, upon arrival at the deployment level, the entire system (the
ROV with all auxiliary systems and the garage) was required to remain in place foe a period of time (less than 30 minutes) in order to allow the INS to settle and to pro- gram the INS with the starting coordinates of assumed at the center of the garage within the shaft.
After calibrating the INS, positioning and orientation required that the ROV back out from the garage towards eastbound drift, circle 180 degrees around the garage, and then navigate to the westbound drift. After 100-ft. of pen- etration down the westbound drift, passing an oversized tool storage closet and arriving at an intersection of tun- nels, the ROV had to turn 90-degrees to the north and perform an additional 230-feet penetration to get to the bulkhead door to be inspected.
Accomplishing this required that the ROV negotiate past a Bobcat skid steer tractor, a number of cables, pipelines and other infrastructure hanging from the tun- nel ceiling, and finally maneuver past a scoop loader (low profiler tractor used in mines) that the miners had been using to try to pull the bulkhead door shut immediately prior to evacuation from the flooding mine. Finally, the
ROV was to take a video survey of the bulkhead door which, due to the poor visibility, required that the camera be positioned very close to the door and associated slings.
In approximately 1525-ft. of water, with near zero visi- bility, the imaging sonars were necessary for general obsta- cle avoidance, and the additional pan/tilt cameras provid- ed improved field of vision, but the 2D and 3D models in
Hypack, with the real-time navigation input from the
INS, provided the SeaView Systems' ROV operator with a real-time global picture of the progress of the venture from the deployment garage to the targeted bulkhead door. Leaving the garage, it soon became apparent that the 3-D virtual guidance was a great aid to the pilot and lived up to its promise in allowing the mission to be flown in virtual space as the ROV traveled in real space. The navi- gation and obstacle avoidance was complimented by the three sonars also carried aboard the ROV.
Hypack's 3-D Terrain Viewer also added the flexibility of changing the viewing perspective, such that you can view progress in the 3-D environment from several differ- ent camera settings. We found that operating from within the survey vessel (in this case, the ROV), or from just behind and above the ROV, to observe challenging, pre- cise maneuvering, to be the most valuable approaches.
Also, to avoid entanglement, SeaVision was able to maintain the overall tunnel in two critical ways: first, to place concept models of large obstructions into the model so that they could be avoided during egress, and second, to record the track taken into the tunnel in order to devel- op a "Hansel-and-Gretel" trail that could mimicked on egress. Both capabilities provided specific additional means of umbilical management to complement the over- all dramatic improvement in situational awareness in this confined access situation fraught with entanglement haz- ards.
Continued improvements in video and sonar technolo- gy are helping to improve the quality of visual feedback in
MTR#4 (17-32).qxd 5/13/2008 10:01 AM Page 30