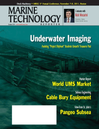
Page 44: of Marine Technology Magazine (October 2011)
Ocean Engineering & Design
Read this page in Pdf, Flash or Html5 edition of October 2011 Marine Technology Magazine
44MTROctober2011 ing operations and less people required for operations. Over the course of a project, it is difficult to avoid some periodic recovery of underwater equipment for mainte- nance or adjustment purposes. If a plough needs to be recovered between towers, it will leave exposed cable or else the entire cable section may need to be recovered and ploughed in again, starting all over, requiring more time cable handling personnel. Any ?plough-ups? or anomalies not corrected at the time will require PLIB by a trenching ROV. A trenching ROV, on the other hand, can be quick- ly recovered ? usually by a single man if needed. This makes it easier to repair or adjust nozzles or jetting arms in mid-operations. The arms of a jetting trencher do not need to be ?loaded?. The product cable can then be re- captured by lining up and lowering the jetting arms around the cable. It?s probable that every wind farm plough job will need some form of PLIB to remedy these unburied situations. Exposed cable, slack, bends and loops are best buried with a jetting ROV while a mechanical cutting ROV would introduce too much risk of damaging the cable. Older Equipment While older systems may provide some advantages (low acquisition cost, etc.), the age can present some major lim-itations. For example, vehicles built for deeper telecom work are typically rated for 2500 to 3000 meters of sea- water depth. They are designed to work with smaller diameter cable and can be vastly underpowered for deal- ing with the larger diameter and heavier power cable. Also, their larger flotation profile creates problems in the high-current, shallow waters typical of wind farm sites. In addition to the limitations of their technology and design, one-off and older legacy systems can also present a myriad of potential operational problems. Finding experi- enced operators familiar with the operating system may behighly difficult or even impossible. Outdated procedures and unique system idiosyncrasies become an issue. Plus, spare parts can be expensive to procure, and difficult to source. With the well-defined unique cable burial equip- ment requirements of inter-array cable, it is clear that new systems must be designed to meet the technical and capac-ity requirement demands unique to the OWF industry. New Equipment When a vehicle is specifically designed and purpose- built, certain design consideration and economies can beleveraged to reduce the overall acquisition, lease and oper- ating costs. Here we outline some specific areas that an operator should consider when selecting a trenching vehi- cle or tool specifically for the installation, trenching, bur- ial, surveying and future maintenance of power cables within the OWF market. Maneuverability Typically, wind farm sites are located in relatively shal- low, high current, windy and rough waters, with a limited or seasonal weather window for installation and mainte- nance. Weather downtime caused by adverse conditions can run as high as 40% at the height of the season. These challenging environments can bring a project to a stand- still until they improve. Being able to expand the weather window has huge implications to the project?s bottom line. Holding up an expensive ship and crew operation because of vehicle limitations can cause expensive delays. If these delays add up, they can domino to other even more expensive turbine installation vessel activity in the broader schedule. Tracks Sea bottom conditions can even vary within the space of a single wind farm. Though some ROV?s are made to free fly by adding buoyancy, trenchers can actually benefit from negative buoyancy that allows jetting forces to cut into the sea floor. Larger capable tracks will allow the trencher to traverse undersea terrain ranging from softer muddy bottoms to steep inclines, as well as being better able to negotiate obstacles.Alternatively, trackless ploughs use skids that can have a tendency to ?run away? when aimed down a seabed incline. As the seabed gets harder, ploughs are also increas- ingly difficult to steer. It becomes critical to manage any sea floor slope and maneuver around problematic bottom terrain.Thus, the ideal IA vehicle would be a powerful tracked vehicle that can be maneuvered even during high currents. A low and wide profile aids in stability and can allow the vehicle to continue to work longer in adverse tidal or cur- rent flows. Commercial-Off-The-Shelf Parts ? COTS Burial equipment manufacturers tend to incorporate proprietary parts into the construction of their vehicles. These unique parts can cost more to replace, as they are not mass-produced. This can also cause long lead times when ordering spares from the original equipment manu- facturer (OEM). There is also a risk that the part will not be available when necessary. The problem of discontinued MTR#8 (34-49):MTR Layouts 10/10/2011 11:38 AM Page 44