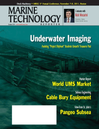
Page 45: of Marine Technology Magazine (October 2011)
Ocean Engineering & Design
Read this page in Pdf, Flash or Html5 edition of October 2011 Marine Technology Magazine
www.seadiscovery.com Marine Technology Reporter 45parts can be crippling, especially with some electronics components. For example, replacement control boards are costly and hard to find if the technology is obsolete. Using off-the-shelf parts can increase versatility and be a key component in reducing overall operating costs. Jetting For soil conditions from 5Kpa to 120kpa, the optimal method of burying a cable is to jet water into the sea bot-tom to ?cut? a trench for the cable to settle into. Because the sea floor can be studied from the pre-project surveys, this process should be pre-planned to utilize the best jet- ting swords and nozzles for the soil conditions. Mechanical cutting (as discussed above) with a chain or wheel is another method utilized when the sea bottom conditions are too hard for jetting. However, this mechan- ical cutting has other intrinsic problems ranging from clogging, fouling and maintenance down time, to a high- er risk of accidental damage to the product cable itself. The ability to control the jetting force is very important. Some jetting systems are either ?on? or ?off,? and in the case of jetter power, bigger is not always better. Too much power can result in cable trenches that are too wide and therefore self-defeating. If the resulting trench ends up being simply a large ditch, the product cable can still be exposed to anchors, fishing nets and other hazards. One method that has proven effective in gaining control over the jetting force is to employ a variable speed motor that drives the water pumps supplying the jetting force. Varying the driver (and therefore the jetting force) allows the operators to ?fine-tune? the process to compensate for variances in soil conditions. Versatility A versatile trenching vehicle can also be used for ?multi- tasking? while expensive vessels are deployed. An OWF installation involves many ships that are performing inter- dependent operations. One ship can easily be delayed by having to wait for another ship to complete its activities.Therefore, it is highly beneficial if the ROV host ship can convert any ?down time? to productive work while it is waiting for another ship to finish its work. Some other tasks that a trenching ROV can also perform are: Post Lay Inspection & Burial (PLIB), Pre Lay Surveys (PLS), Touch Down Monitoring (TDM), foundation scour surveys and cable maintenance. Often, PLIB work will be required after a plough is used to bury cable. The ?plough up? and ?plough down? oper- ations will leave sections of the cable exposed at each end of the run and at any cable crossings. Returning with a jet- ting trencher at some point may be the only way to com- plete the burial. Fortunately, the final ?as built? survey data could also be collected at this time as well. A trenching ROV can also be used to perform various other operations if fitted with the correct equipment. With its robotic arm, the ROV operator could assist with feeding the cable pull-in at the J-tube. Special tooling is also used to perform and ?cut and grab? that allows the vessel to pull up and retrieve problematic cable. Power Nameplate data does not always translate to available power for specific operations. When considering the trencher power, calculate the resulting power that is actu- ally available to power the tracks, water jets and ancillary equipment. In surface fed units where the water pressure is actually generated on the surface, the power available for water jetting on the sea floor is inversely proportional to the water depth. In addition to the extra piping losses, you will generally loose 1 bar (15 psi) per 10m (30 feet) ofwater depth. Attempting to do work too deep will be slow or fruitless. Operating Depth As most wind farms today are sited in 10 to 40 m of water, a long expensive umbilical is not needed. Often, repurposed systems will have existing umbilical capable of 2500m water depth operations. Longer umbilicals caneven impair shallow water operations, as the remaining wound umbilical can actually heat up on the winch reel. ConclusionDue to unique physical constraints of OWF arrays and the sensitive nature of the power cable, as well as the repet- itive nature of multiple turbine connections, the favored method for inter-array cable burial is PLIB trenching with a tracked vehicle. Additionally, when seabed conditions allow, water-jetting technology is preferred over the poten- tially more dangerous mechanical cutting. Our research shows that many burial vehicles will be needed as OWF build rates increase to meet industry projections. If burial equipment is available, its owners will probably be using it in their bid proposals for upcoming jobs. It will be the responsibility of the hiring company to perform sufficient due diligence to ensure that the equipment proposed is the best suited for the job. Email: info@ pharos-offshore.com www.pharosoffshoregroup.com MTR#8 (34-49):MTR Layouts 10/10/2011 11:38 AM Page 45