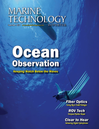
Page 55: of Marine Technology Magazine (September 2014)
Ocean Observation: Gliders, Buoys & Sub-Surface Networks
Read this page in Pdf, Flash or Html5 edition of September 2014 Marine Technology Magazine
est standards under ISO 9000-2008. Each machine is hand assembled and built with the fi nest materials including high strength aluminum, epoxy coated syntactic fl otation, high al- loy stainless steel, bronze and heat treated carbon steel with protective plating. As the CPT will be used almost exclu- sively in salt water the machine includes integrated cathodic protection. Every part on Wachs Subsea’s CPT is designed to resist corrosion and require minimal maintenance.
The machine’s hydraulic and electrical systems are equipped with depth compensation for deepwater opera- tion under extreme pressure, and each includes an advanced warning system to alert the operator if seawater infi ltration is detected. While primarily developed for deepwater opera- tions it’s worth noting that the CPT series is equally suitable for shallow water operation, in keeping with the industry trend of keeping divers out of the water and out of harm’s way. The CPT-3 and CPT-4 will function equally well in 30 meters of water as in 3000 meters.
Another feature worth noting is the machines ability to perform on near vertical work pieces. With its centralized center of gravity plus it’s near neutral buoyancy it’s an easy maneuver for the ROV operator to position the CPT on a pipeline ascending or descending even the steepest seabed feature.
Deploying the machine begins by positioning the CPT in its custom deployment frame on the seabed, in close prox- imity to the repair site. The CPT clamps securely to a center fi xture on the frame for transport and storage. The deploy- ment frame features a single pivot arm for ease of lowering and lifting, and a mudmat to prevent stiction on the seafl oor and to minimize silt clouding. As pressure compensation is integrated into the CPT, the deployment frame requires no additional compensation.
The CPT-3 is compact and light enough to be deployed with a wide array of ROV’s, and is energized and powered by the ROV via electrical and hydraulic zero leak hot stabs.
The pipeline repair begins with the ROV pilot removing the
CPT from its deployment frame, then fl ying and clamping it on the damaged pipeline near the initial cut line. The CPT
Severing/OD Chamfer module performs the fi rst severing operation. Its hydraulic autofeed system produces pinch-free severing with a smooth, controlled cutting action suitable for pipelines under light compressive loading. For heavy compressive loading some manner of subsea pipe handling equipment (by others) is recommended. Wachs CPT-3 has been successfully integrated into several manufactures pipe lift systems.
The CPT is then transited to the second cut line, where the operation is repeated. The replacement jumper spool sec- tion, following metrology measurements, is typically fab- ricated topside at this stage and made ready to lower to the seabed. Following removal of the damaged section the CPT chamfers the pipe OD to prevent sleeve connector damage www.marinetechnologynews.com
Marine Technology Reporter 55
MTR #7 (50-65).indd 55 8/27/2014 12:15:56 PM