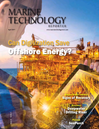
Page 36: of Marine Technology Magazine (April 2017)
Offshore Energy Annual
Read this page in Pdf, Flash or Html5 edition of April 2017 Marine Technology Magazine
Global Finite Element Analysis of drilling riser.
ages to develop the optimum design. This effort is re? ected ing transferred to subsea equipment and conductor casing in a solution that corresponds to a minimal loss of buoyancy programs from the riser. Overall decreases in cyclical loading uplift, due to a minimal removal of material to facilitate the may lead to increases in the integrity and life span of critical inlaid groove, while still retaining vortex suppressing proper- well containment equipment. Possible bene? ts of the reduc- ties. Similar to external strakes the inverted design disrupts the tion of riser drag and VIV by means of reengineered drilling continuity of ? uid ? ow around the outer diameter of the buoy- riser buoyancy are numerous, with the potential to enhance ancy modules by introducing variances in the cross-sectional overall performance of drilling vessels and the economic fea- geometry at each new cross section along the axis of the riser. sibility of accessing reservoirs in increasingly challenging en-
Discontinuities in external geometry pro? les along the axis of vironments.
the riser lead to variances in the separation point of the ? ow Drilling operability envelopes, or the connected vessel dis- around the outer diameter of the drilling riser which disrupt tance away from directly over wellhead that is still deemed the organization of forces due to vortex shedding, the driving safe to drill, are frequently limited by allowable mean and force responsible for larger magnitudes of riser response and maximum ? ex joint rotation angles, requiring the suspension subsequent dynamic strain. of drilling activities at higher rotations. With a decrease in
Three dimensional ? nite element models developed for use the in-line drag loading and overall de? ection of drilling riser in CFD analysis help to illuminate additional bene? ts realized systems, upper and lower ? ex joint rotations are reduced for from the inverted helical design. In contrast to traditional buoy- certain environmental conditions and riser system con? gura- ancy modules where ? uid ? ow paths occur almost exclusively tions. This can correspond to increased time frames where in the horizontal plane, looking down the axis of the riser, axial rotation of the drill string within the riser annulus is permis- ? ows induced by the inverted helical groove introduce turbu- sible, without the danger of key seating the riser joints. This lence into the downstream wake pro? le of the drilling riser. potentially allows offshore wells to be drilled faster as win-
Axial ? ow paths result in forces that act out of plane of cross dows of time where operations are suspended due to riser de- ? ow lift forces and in-line drag forces disrupting the cyclical ? ection are diminished. rotation of these forces on the downstream side of the riser. Bene? ts extend beyond the expansion of drill string rotation envelopes; decreased in-line drag and riser de? ection can en-
Reducing VIV and Inline Drag able deployment and retrieval of the riser in higher current envi-
Reduction of riser motion due to VIV in the in-line and ronments. Additionally, reductions of overall de? ection along cross-? ow directions can limit the amount of dynamic load- the riser can lead to a reduced possibility of clashing between
April 2017 36
MTR
MTR #3 (34-48).indd 36 MTR #3 (34-48).indd 36 3/30/2017 11:05:50 AM3/30/2017 11:05:50 AM