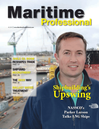
Page 47: of Maritime Logistics Professional Magazine (Q4 2013)
Shipbuilding, Repair
Read this page in Pdf, Flash or Html5 edition of Q4 2013 Maritime Logistics Professional Magazine
With all these beneÞ ts, the use of 3D Laser Scanning, de- spite its availability, nevertheless has not become a main- stream practice in ship repair and retroÞ t operations. The reasons why come down to three main issues. These include cost of hardware, capability and difÞ culty of use, computing power limitations and inconsistent workß ow and software so- lutions. Fortunately, most of these issues have been addressed, as depicted below: 1. Hardware Cost and Dif Þ culty of Use Until recently, laser scanning equipment was cumbersome (multiple components with total weight over 150 lbs) expen- sive ($150,000+), requiring highly skilled crews to operate. With the recent offerings from FARO, however, the new Fo- cus3D scanners weigh in at just 12 pounds, at about one-third the cost and are similar in operation to a high end digital cam-era. The new scanners can, with one person, take signiÞ cantly better measurements in one day than a Ôship checkÕ team can accomplish in a weekÕs time. More signiÞ cant, perhaps, is that every vessel can perhaps justify having a scanner on board, al- lowing the Chief Engineer or Project Manager to direct work in detail within 3D model shots of his machinery spaces. With this approach, the cost required to obtain accurate measure-ments has been greatly reduced Ð and can be accomplished from far out to sea, well in advance of the repair procedure. 2. Computing Power Limitations Another barrier to wide acceptance of 3D Laser Scanning was the huge data sets that bog down computers and made it dif- Þ cult for managers to visualize their projects in the 3D Point Cloud. Autodesk ReCap and Bentley Pointools among others have and are making great strides to overcome this barrier. 3. DifÞ cult Work ß ow and Software Solutions The next limiting factor is the work ß ow and software that al- lows CAD Designers to work directly in the 3D Laser Scan Point Cloud model and apply statistically valid algorithms to the point cloud data for feature extraction of system components such as piping, structure, and more. The software available on the market to meet this need has grown considerably over the last few years and is available from such companies as Kubit, Innovmetric, Edgewise and Kohera3D Ð just to name a few. ?We Haven?t the Money, So We?ve Got to Think? It was Ernest Lord Rutherford who is credited with saying, ÒWe ha venÕt the money, so weÕve got to think.Ó A renowned Physicist, Rutherford proved time and time again that thinking saves money, but what drove him was his love of solving prob- lems in more efÞ cient and cost effective ways. The new 3D laser scanning technology is the perfect Þ t for this way of thinking. In 2007, Summit Engineering and Design, LLC moved to FARO scanners and at the same time, began to develop soft- ware solutions so CAD designers could work directly in the Point Cloud model. Summit had learned the hard way that the further away from the Point Cloud the designer was removed, the more likely simple, yet costly design mistakes would be made. Data sets were needed that (a.) AutoCAD could handle, (b.) would allow clients to direct their project scope, and (c.) allow all to see the progress of the design efforts. Ultimately, this led to the ability to isolate (or classify or segment) the DESIGN TECHNOLOGYLayered and decluttered 3D Point Cloud model used to visualize and deÞ ne scope Non-layered 3D Point Cloud model of machin- ery space to be retroÞ ttedwww.maritimeprofessional.com | Maritime Professional | 47MP #4 34-49.indd 47MP #4 34-49.indd 4712/11/2013 1:32:58 PM12/11/2013 1:32:58 PM