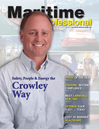
Page 51: of Maritime Logistics Professional Magazine (Q1 2014)
The Energy Edition: Exploration, Production & Transportation
Read this page in Pdf, Flash or Html5 edition of Q1 2014 Maritime Logistics Professional Magazine
FLEET OPTIMIZATION
For the handful of shipping companies to date that have de- cided to try navigation as an alternative to drowning in their rising ocean of data, it’s not hard to fi nd examples of what the right kinds of decisions can get you. For example, monitor- ing can mean the difference between a successful voyage and coming to a dead stop somewhere in the middle of the deep blue because you didn’t know how to read the data points tell- ing you over the last two weeks that an engine breakdown was imminent. (Heading off system failure is one of the two top reasons users are attracted to data analytics; cutting fuel costs and consumption is the other.)
Or, in the case of an offshore supply vessel, the decision to compare the difference in exhaust temperatures between cyl- inder banks at different operating modes. This led that compa- ny to make a simple, yet timely repair, which prevented a po- tential future failure that ESRG says could have cost $750,000 in repairs and downtime.
Then there’s the kind of decisions that enabled Bernhard
Schulte Shipmanagement (BSM) to achieve a 2% to 5% re- duction in fuel consumption three years into its fi ve-vessel
ESRG real-time data analytic installation. It doesn’t sound like much, but in actuality, it adds up to a lot more than chump change. As explained by project manager Romuald Wojtaszc- zyk, who held a variety of positions at BSM over a 24-year career, most recently as project manager for its ESRG install, before moving to Nordic Hamburg Shipmanagement to work on another ESRG project, “If consumption is 100 tons a day, and you are able to save 5%, and if the price is $500-$600 per ton, now you are saving $2,500 a day. If you calculate for the month, now it’s $75,000. Money like that cannot be ignored.”
That’s exactly the kind of fuel optimization and effi ciencies- related savings that American Roll-on Roll-off Carrier (ARC) thinks is realistic, and hopes to achieve as it pilots ESRG’s
OstiaEdge package on a single vessel. If all goes well, ARC will expand the software to the rest of its seven-vessel fl eet later this year. “We are looking for a nominal improvement in fuel con- sumption – 2% to 4%,’’ says Fred Finger, vice president & general manger, FLP and Vessel Operations at American Roll
On Roll Off Carrier. “We’ll be happy if we get an incremen- tal increase in vessel reliability and reduce off-service time by 5% to 10%. Then as we see what the capabilities [of the system] are, we’ll have a better idea of where to go beyond that. Right now, we are being very conservative in our expec- tations, but if the system works as we expect, our payback will be well less than a year.”
Condition-based maintenance is also paying off for com- panies like BSM. For example, Wojtaszczyk explains how something as simple as looking at the bearings on the shaft of an electrical motor can lead to savings. “The recommen- dation was to change them out every one and half years. We were fi nding that the bearings at that point were still very well conditioned. But if you take them out, you cannot put them back in. You have to install new ones.” Using CBM, BSM dis- covered it could wait two and half years before replacing the bearings – saving time and money.
And in cases where equipment maintenance schedules are mandated by class rules, users can take the historical data from CBM to the classifi cation society and request that it ex- tend the maintenance intervals for that piece of equipment.
The opposite situation is true as well. Companies can bring historical records that show underperforming equipment to manufacturers in a bid to seed corrections, and also use those records to make new equipment or maintenance allocation choices for their fl eet.
It can be hard to compare equipment use across a fl eet with ves- sels of different ages, running different routes, dealing with dif- ferent environmental issues. But data analytics can nonetheless ferret out trends that show some brands or types of equipment are more problematic than others. “So when you make plans for
Understand equipment energy effi ciency: Using ac- tual engine performance and fuel consumption to target maintenance when and where needed.
Optimize Generator confi guration: Using actual generator fuel performance to optimize the con- fi guration based on the current electrical load. www.maritimeprofessional.com | Maritime Professional | 51
MP Q1 2014 50-63.indd 51 2/26/2014 1:33:43 PM