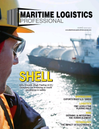
Page 40: of Maritime Logistics Professional Magazine (Q3 2016)
Shipbuilding, Repair & Maintenance
Read this page in Pdf, Flash or Html5 edition of Q3 2016 Maritime Logistics Professional Magazine
INTERVIEW
Torinia off Gibraltar leaks.” It is critical that our employees, contractors and part- routing eastbound ners in safety embrace and believe that Goal Zero is possible.
Anything less is unacceptable.
July 13, 2007
Is there one style, one mode of learning that
Shell Shipping holds above all of the rest?
One of the greatest challenges for any global business that seeks to build a culture of safety is the penetration and effec- tiveness of learning, measured by whether it actually chang- es behavior. This is particularly true in the maritime realm, where crew rotation, shift work and distance from manage- ment makes it dif? cult to reach everyone. There is evidence that the traditional methods of delivering safety messages and learning from incidents – such as ? eet notices, safety alerts, safety meetings and tool box talks – are not having the desired outcome in changing people’s deep seated behavior and mind- set in preventing similar future incidents from happening. For example, people continue to die or sustain serious injuries in mooring accidents or working in con? ned spaces. These in- cidents too often share common causal factors that are well documented in the lessons learned from previous incidents.
Shell has adopted re? ective learning as a means of making a step change in learning from incidents (industry evidence in- dicated ~70% content retention compared to <10% retention when using existing communication tools). Re? ective learn- ing uses simple and engaging materials, such as video, in a fa- cilitated, interactive group setting. The objective is to focus on the important themes, drawing out personal experiences from participants, in a way that creates behavioral change. This type of structured, face-to-face engagement has been shown to be more effective than lectures, reading or brief tool box talks or safety meetings.
The typical re? ective learning session lasts about an hour and involves 20 to 30 participants. A trained facilitator starts the session with a discussion of barriers, and then uses a video that describes a scenario developed from one or more actual incidents. The video is paused at key points and the group di- vided into teams to consider questions posed by the video nar- rator. These discussions are the key to the success of re? ective learning, and the facilitator plays an important part by keeping the teams focused, drawing out personal experiences for shar- ing, and helping them identify factors within their control that will make barriers on their own vessels more effective. The video is re-started after each pause and more information pro- vided. Most important, the session concludes with the partici- pants identifying and committing to actions to make barriers more effective on their vessels.
Shell is helping improve industry safety by providing fa- cilitator training and producing re? ective learning videos and written ‘Learnings From Incidents,’ which are shared through the Shell Partners in Safety program.
40 | Maritime Logistics Professional | 3Q 2016 34-49 Q3 MP2016.indd 40 8/17/2016 10:32:59 AM