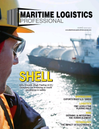
Page 49: of Maritime Logistics Professional Magazine (Q3 2016)
Shipbuilding, Repair & Maintenance
Read this page in Pdf, Flash or Html5 edition of Q3 2016 Maritime Logistics Professional Magazine
“These people have succeeded in a dif? cult environment – the military – and have more discipline and leadership capabilities. They know their way around a ship, all the ter- minology, how to deal with the customer, how they think.
We could not run NASSCO without hiring former military.” – Kevin Mooney,
Vice President of Programs and
Supply Chain Management cars just to be able to be there to do the classes. They get teary- ing, committed to what is a physically demanding career path, eyed because they know they had nothing to look forward to,” and in some cases, come with years of experience working says Rick Biben, president of Gibbs & Cox, Inc., who is on as welders, machinists and fabricators on ships. They know two WFW boards. With 2,500 openings in the area per gradu- where the piece they are making is going, and they know how ate, “over 90% are hired before they graduate,” he adds. key precision work is, says Michael Bice, president of Vortex
Engineering, because they know what it’s like to have to daily
A Hero’s Welcome on the Shop Floor use a poorly made locker or desk, etc..
You don’t have to ask employers like NASSCO, GD BAE “They have the ability to learn and improve,” says Bice, ex- and Vortex Engineering twice to hire a vet. “Students out of plaining that “you spend the whole time in the military train- high school are looking for a ? rst job. These [veterans] have ing to get better.” For example, a welder he hired from WFW experience, training, maturity. As an employer, I’ll take that had an ‘okay’ skill level, but his “real value,” says Bice, was any day of the week,” says Biben. his willingness to listen to the more experienced workers on
Beyond patriotic sentiments, there are many reasons why the shop ? oor helping him grow as a skilled craftsman.
ex-military would be in high demand for advanced manufac- “It takes all those years of knowledge to be passed on from turing positions, say BAE’s Elden and Kevin Mooney, another one person to the next to actually be the best at what you do. If
Navy veteran and vice president of programs and supply chain we could get young America working side-by- side and transfer management, NASSCO. Both are WFW supporters. that knowledge, it would be most bene? cial. I am worried about “These people have succeeded in a dif? cult environment – that gap; every year we delay, it makes it harder,” says Elden. the military – and have more discipline and leadership capabil- The ? y in the ointment is that WFW can’t graduate enough ities. They know their way around a ship, all the terminology, workers fast enough to meet demand – from students or em- how to deal with the customer, how they think. We could not ployers. It’s why Eden thinks the maritime industry should run NASSCO without hiring former military,” says Mooney. provide a certain amount of tax-deductible ? nancial aid to “It is extremely dif? cult in San Diego to ? nd someone who WFW, who can turn out more skilled workers at a lower cost can machine or weld, never mind both,” says BAE’s Elden, than apprenticeship programs and give the supporting compa- who says shipyards and defense contractors often have to tell nies ? rst access to job interviews. the government that they will have to delay work processes or The best thing, though, says Elden, is what the program repairs because they don’t have certi? ed welders. does for the students. “Early in the program he sent me pic-
BAE subcontracts work to WFW Industries, and sent two tures of students – two were in wheelchairs with no legs, one workers through the program, effectively paying for an entire was missing an arm. These people that have given so much to class, in part to “help keep the doors open” in the school’s the country, graduated and were placed in jobs, but without early days in San Diego. Beyond that, says Eldon, “We do Hernán, they’d be lost. I don’t know how you put a price on $100,000 worth of work a year through the pro? t side.” that. It’s life changing. It’s why I stay involved.” And it’s why “When you hire a veteran that’s gone through his system, Work Shop For Warriors hopes you will too. you get someone who steps on the property ready to go to work, comes with the certi? cations that you need, and who
Patricia Keefe has that level of dedication to the trade that you need for them is a veteran journalist, editor and commen- and your business to be successful,” Elden notes. tator who writes about technology, business
Unlike high school-aged apprentices or vocational or col- and maritime topics. lege graduates, most veterans are older, used to problem-solv- www.maritimelogisticsprofessional.com 49I 34-49 Q3 MP2016.indd 49 8/17/2016 10:44:32 AM