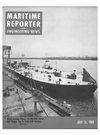
Page 31: of Maritime Reporter Magazine (July 15, 1969)
Read this page in Pdf, Flash or Html5 edition of July 15, 1969 Maritime Reporter Magazine
Pacer-Class Design (Continued from page 32) Helical Ship?The helical ship is a patented form consisting of flat plates, plates with curvature in a single plane and rectangular sections with the exception of the bow and stern underwater portions which are helical in shape. Preliminary resistance tests on a hull of this type built to Mariner proportions in-dicated an increase of about 20 percent in ehp compared to the Mariner parent. The question of the true magnitude of the possible life-cycle cost savings to be realized by the use of simplified forms is yet to be re-solved. Meanwhile the preliminary design has been completed using the conventional round-ed parent form. Structural Hull The hull structure is typical of modern car-goliners, with the top and bottom flanges longitudinally framed and the side shell and intermediate decks transversely framed. Mild steel is used throughout without a reduction in thickness for special coatings. The inner bottom plating is all of one thickness in order to minimize the number of plate sizes. To avoid the necessity of normalizing, the maxi-mum thickness of plating specified is l^g inches. With the exception of the gunwale con-nection to the sheer strake, the hull is all welded construction. The twin hatches are framed with three longitudinal girder systems supported by col-umns at the hatch corners. The hatch end beams extend to the shell to form part of com-plete transverse webs. Bilge brackets have been eliminated at the expense of heavier hold frames in the interest of conserving deck area for cargo stowage. Superstructure?The superstructure was de-signed to basic needs only with a view to sym-metry and simplification of construction and minimum maintenance. Such items as curved bulkheads, recesses, and offsets, have been virtually eliminated. The number of exterior doors and inclined ladders has been held to a minimum and deck overhangs eliminated to the greatest practicable extent. The quarters comply with current commercial standards of habitability. All living and public spaces are air conditioned and single occupancy rooms are provided for the entire crew. Cargo Handling Cargo handling function is so basic to the economic success of the ship, care had to be exercised that cost reduction would not seri-ously impair the operating efficiency. The twin hatch arrangement provides multi-ple access to the cargo stowage spaces and at the same time leaves ample shelf space which is so important in multi-port trade routes. The main hatches are arranged for stowage of 20-foot containers in the athwartship posi-tion. The loaded containers can be either han-dled by a marriage of two 10-ton booms or by the 70-ton and 30-ton Stulcken gears located between holds Nos. 2 & 3, and 4 & 5. Forty-foot containers can be stowed in a longitudinal position in the four hatches served by the heavy-lift gear. One of the most expensive items in the out-fit is power-operated hatch covers. A rather substantial saving has been realized by specify-ing mechanical covers of an advanced type successfully installed on a class of recent sub-sidized ships. The prevalence of a-c cargo winches on for-eign-flag ships led to a review of the long standing MarAd practice of specifying d-c winch drives with variable-voltage control. It was concluded that satisfactory control could be achieved with a-c drive. However, inquiries directed to manufacturers revealed that no do-mestic supplier could deliver a-c drive cargo winches without some development work. Opinions on cost varied widely. In view of the uncertainty of supply, d-c variable voltage drive is specified with a-c drive permitted as an alternate. Table 2?Cost- Reductions Group Cost Reduction 1. Steel $ 300,000 2. Accommodations and ventilation 300,000 3. Hull piping 375,000 4. Electrical and electronics 350,000 5. Deck outfit 225,000 6. Cargo handling and deck machinery 700,000 7. Cargo refrigeration 550,000 8. Machinery 575,000 9. Indirect charges 75,000 Total Reduction $3,450,000 Steam Plant The major features for the Pacer main ma-chinery plant had their origins in two study contracts undertaken by Newport News Ship-building and Dry Dock Co. and the J. J. Henry Co., Inc. for MarAd's Office of Research and Development. Additionally, the design reflects somewhat the experience gained at MarAd with respect to maintenance and repair costs and frequency of occurrence and some of the basic ideas put forth by the Humble Oil Co. in the construc-tion of the Esso Houston class of tanker. Out of the above sources, the design is be-lieved to have achieved the basic goals of pro-viding a reliable marine propulsion plant that meets the qualifications of: minimum capital cost, noncomplexity of machinery installation and operation, and adaptable to commercial requirements. Steam conditions for the Pacer design have, basically, been selected in accordance with the findings of Newport News Report MA-2967. This study considered steam conditions from the standpoint of initial cost of pressure and temperature, dependent materials, plus present worth of fuel costs and maintenance over the lifetime of the ship, and concluded that steam conditions of 600 psig and 850°F. were eco-nomically attractive. Superheated steam is supplied to a conven-tional cross-compound propulsion turbine and the one operating turbo-generator which ex-hausts to the main condenser. The deaerating feed heater uses bleed steam from the cross over. No other feedwater heating is utilized except in the boiler economizers. This cycle reduces capital costs and provides simplified installation and operation. There is some sacrifice of fuel consumption to achieve the design goals. However, the fuel performance is still a respectable 0.541 lb. per shp-hr and compares favorably with many ships built under MarAd's ship-replacement program. f Single Boiler Concept?The obvious pre-liminary choice for one boiler was made after subjecting the proposal to an economic evalu-ation. It was also decided to incorporate some form of take-home capability mostly to pacify the persistent skeptics. Take-home Power?A simple packaged boil-er was selected on the basis of cost and the need for hotel service steam when in port when operating the standby ship's service diesel-generator set. Electric-Plant?The design concept of the ships-service electric plant was to provide adequate but not excessive capacity. An al-lowance for the carriage of 20 refrigerated car-go containers was made. A preliminary electric load analysis showed a maximum port load of 646 kw and a maxi-mum sea load of 592 kw. The selected electric plant consists of a 750-kw turbo generator for both at sea and in-port use and a 600-kw die-sel generator as a standby. The standby unit rating of 600 kw was chosen on the basis that if needed, certain un-essential loads could be dumped and others limited. Manning and Mechanization?The scope of plant mechanization is limited to that which is necessary for safe and efficient operation with two watch-standing personnel. The boiler is fully mechanized in accordance with the ap-plicable USCG regulations for a two-man watch. No other mechanization such as bridge control of main engine, automatic data logging and bell logging is provided. Some large valves will be provided with motor operators. A cen-tralized control console incorporates boiler and turbine throttle controls at a convenient op-erating station. Other console display and con-trol functions are limited to those necessary for maneuvering the vessel. Additional Cost Reductions in Machinery? The specifications for the steam plant machin-ery contain several items which can also sig-nificantly contribute to overall cost reduction. Among these are the requirements for highly loaded main reduction gears, high boiler heat release rates, dripproof electric generators in lieu of enclosed air-cooled types for standby units and all cognizant MarAd value engineer-ing letters. Table 3?Multiple-Construction Cost Each Of Steam Diesel 1 $17.1M $16.5M 2 15.6 15.0 3 14.8 14.3 4 14.3 13.8 5 13.9 13.4 10 12.8 12.4 15 12.3 1 1.9 20 1 1.9 1 1.5 25 11.7 11.3 Diesel Plant Selection of Engine?At the outset of the diesel-propelled design it was decided that the existing steam-plant machinery space would remain intact and the highest horsepower die-sel propulsion unit that the engine room and machinery casings could accommodate would be installed. The limiting machinery dimen-sions ruled out the possible use of high horse-power slow-speed, direct-connected engines. Engine selection, therefore, was limited to compact medium speed engines. Of the avail-able diesel engines, a 1,250 bhp/cylinder model offered the best horsepower per cubic foot needed to fulfill the design criteria. Final selec-tion depended upon whether a single V-12 en-gine or twin, "in line 6", engines would be more desirable. The twin engine concept was chosen based upon the advantages of (1) in-creased reliability and (2) easier maneuver-ability; with minimum increase in capital cost. The engines selected would not produce the same power and speed as the steam turbine version, however, the total output of 15,000 bhp would suffice to obtain 19.4 knots speed. The small sacrifice of 0.6 knots was considered acceptable to obtain a viable diesel design. Costs Having taken advantage of all the cost re-duction possibilities, with the exception of the simplified form, and many other lesser ones too numerous to mention, it is believed that lower costs are possible as compared with the parent design, Table 2. The results of this effort then would permit the construction of fleets of the Pacer design at the unit costs shown in Table 3. These are budget type costs for the steam-ship version estimated at 1969 pricing levels and include allowances for changes under con-tract and owner's engineering and inspection. The diesel-propelled alternate would cost ap-proximately 3 to 3^ percent less than the steamship version. The Pacer design thus ap-pears to be capable of being a profitable in-vestment for some trades as its capital costs are between 75 and 80 percent of those general cargo types having the ultimate in refinement and modernity. July 35, 1969 13