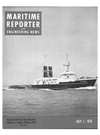
Page 12: of Maritime Reporter Magazine (July 1970)
Read this page in Pdf, Flash or Html5 edition of July 1970 Maritime Reporter Magazine
Trends In Sea-Water Distillation
There Is A Demand For Compact, Reliable And Automatic Sea-Water Distillation Plants
Aboard Ships. During The Last Few Years, The Design Of Such Plants Has Improved
So That Smaller, Less Expensive, Packaged Plants Are Now Available.
J. Herd, C. Eng., M.I. Mech. E„ M.I. Mar. E.*
Although there are several methods by which fresh water can be produced from the sea, in- cluding electro-dialysis, reverse osmosis and freezing, it is distil'ation that is by far the most widely used. Aboard ship it is virtually the only method, although it takes many forms and has advanced to a high degree of efficiency.
In the simplest distillation plant, steam is passed through a heating coil immersed in sea water, which contains about 3.6 percent of dis- solved solids, mostly salt. Part of the water vaporizes, leaving the salt behind, and passes into a condenser while the remaining brine, which has become more concentrated is drawn off and led away.
The term "distilling plant" is applied to the collection of various pieces of equipment which, when set to work together, carry out the com- plete distillation process. For shipboard use such plants have fresh-water production capaci- ties varying from 20 tons to 700 tons or more per 24 hours, and, of course, more than one plant may be fitted into a ship.
Although some ships rely solely on distilled water for all purposes, others use distillation plants to augment water obtained from shore sources and carried in tanks.
Ships in the first category include naval ves- sels which, with their high crew density, lim- itations on weight and space and ever extend- ing operational range, cannot afford large wa- ter tankage. Distillation, therefore, provides the water for drinking and other domestic uses and for feeding the boilers. As water for boilers must have a salt contamination level limited to one or two parts per million, it follows that these ships require a fresh-water making pro- cess which is highly efficient and completely reliable.
The present generation of submarines, being nuclear-steam propelled, and carrying a large complement for extended, totally submerged voyages, also rely on a distillation plant to a very great extent. Such ships clearly do not have the space or buoyancy to spare for carry- ing large quantities of fresh water.
At the other end of the scale, the very big passenger liners will have some water-carrying capacity, though not enough to supply the pas- sengers with all the water they need. With a ship of this type a major distillation-plant fail- ure would make life for the passengers dis- tinctly uncomfortable and would severely em- barrass the shipping company.
The increasing reliance that is being placed on the distillation process is shown by the wa- ter-carrying capacity of two passenger liners.
The Queen Elizabeth, completed in 1940, has tanks for 6,000 tons of fresh water. The Queen
Elizabeth 2 carries only 1,200 tons of fresh *Mr. Herd is chief systems designer, Heat Exchange Div.,
G. & J. Weir Limited, Cathcart, Glasgow, S.4, Scotland.
A Weir remotely controlled MXFR two-stage flash distil- lation plant on test at the Cathcart plant in Glasgow.
Need For Reliability
Because of the growing reliance on the pro- duction of fresh water aboard ship and increas- ing personnel consumption, the primary need at sea is for a simple, efficient and above all reliable distillation plant.
At the same time it is desirable to make use of the waste heat contained in the circulating water system of diesel engines—heat which otherwise is rejected to the sea.
Ships being built today tend to have ma- chinery control rooms with virtually no watch- continued on page 16)
The Weir type MX automatic sea-water distillation plant. 14 Maritime Reporter/Engineering News
The first Weir sea-water distiller, manufactured in 1884. water for approximately the same number of people, but has three flash-distillation plants, each capable of producing 400 tons of water per 24 hours.
F'ash Distillation
Flash distillation is the term applied to the process when the formation of the fresh water vapor occurs at reduced pressure from a brine solution in which no heating element is im- mersed. As in all distillation processes, flash distillation requires the input of heat. How- ever, the heat is imparted to the brine while it is under pressure and, therefore, no boiling takes place at the heat input surfaces.
As a result, all the heat is retained by the brine as sensible heat and it is only when the brine is passed into the flash chamber, which is at a pressure below that equivalent to the brine boiling temperature, that fresh water vapor is formed.
One of the main advantages of this method is that it reduces the formation of salt scale which would otherwise be precipitated by the actions of boiling and brine, and would in time affect the plant performance.
A series of flash chambers can be contained within a single plant. The brine to be evapor- ated flows from one stage to the next at pro- gressively lower pressures. Thus, a four-stage plant would have four flash chambers, gen- erating vapor at say 165° F., 150° F., 135° F. and 120° F.
A four-stage plant has a main ratio of about 2.3:1, i.e. 2.3 pounds of fresh water is produced for every pound of heating steam condensed.
A two-stage plant has a gain ratio of about 1.3:1. These two types present the major pro- portion of the plants supplied.
The vapor generated in each stage is con- densed on condenser tubes in that stage. The latent heat given up by the vapor in condens- ing is used to preheat the brine on its way to the brine heater, where the external source of heat is applied. In this way a marked degree of heat regeneration is achieved and if, in ad- dition to this, some of the residual brine from the last flashing stage is recirculated, then high thermal economy results.