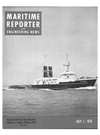
Page 14: of Maritime Reporter Magazine (July 1970)
Read this page in Pdf, Flash or Html5 edition of July 1970 Maritime Reporter Magazine
Sea-Water Distillation— (Continued from page 14) keeping activities in the engine room proper.
Some ships are completely monitored with a comprehensive data and alarm system, and in consequence normal operation calls only for the attendance of a day-work staff rather than the traditional watch and watch system. Mod- ern engine rooms also are smaller. The need has, therefore, arisen for compact distillation plants requiring the minimum of control and maintenance.
These factors have dominated the design of modern plants, leading in some cases to a de- gree of built-in automation hitherto considered impossible to achieve except at heavy cost. The series of MX distillers recently introduced by
G. & J. Weir of Glasgow, Scotland, illustrates this type of plant. The modular design permits the plant to be varied to suit large and small naval and merchant ships. The basic unit can be supplied in sizes producing up to 75 tons per day as standard, but units with larger ca- pacities can be manufactured.
Early Distillation Plants
In an effort to make seagoing vessels inde- pendent of water supplies from shore, the Bri- tish Admiralty ordered in the 1880s a Weir marine evaporator to produce pure distilled water for boiler feed. The first unit was made in 1884. It was successful in operation and larger more complex evaporators followed. A full scale naval plant of 60 years ago included a direct-acting pump, brass-bound wooden casing, and a mass of controls and instrumenta- tion.
It was not until 1959, after much develop- mental work, that the first successful design by this company of packaged distillation plants was achieved. The plant carried out the process at sub-atmospheric pressure, allowing the heat- ing steam to be at lower temperature than in earlier plants and enhancing the temperature difference between heating and heated media for a given pressure difference. For certain ap- plications the process was staged in series to improve thermal efficiency—the vapor genera- ted in one stage being used as the heating medium for the succeeding stage.
Many forms of vapor baffles were used in order to improve further the purity of the wa- ter produced and to increase the stability of operation of the plant. These baffles were of the deflector type, the centrifuge type and a form of fresh water bath through which the vapor passed, being subjected to a scrubbing action to remove entrained droplets of brine.
These plants were heavier, larger and more costly than the new units. Their heating ele- ments had a greater tendency to accumulate scale, and more instruments were needed.
The New Plants
The new MX distiller consists of a set of units which can be assembled in different ways to suit nearly all types of ships. In addition, the traditional array of control instrumenta- tion has been eliminated by automatically con- trolling the various flows. In these ways capi- tal cost is kept to a minimum.
The primary aims when developing these plants were: to design an economical basic unit, to operate at low temperature so reducing scale formation to the minimum and allowing the jacket cooling-water of a diesel engine to be used efficiently as the heating medium, and to provide a completely packaged unit, the op- eration of which would be fully automatic.
In addition, the basic unit had to be: suitable for operation with low-pressure heating steam, capable of remote starting and shutdown, and amenable to batch production, using as many common components over the output range as possible.
The basic unit, which uses a heating element submerged in the brine, had to be designed so that when two of these units are combined, their heating elements can be easily replaced by simple flash chambers which are more eco- nomic in combination. The result is a two- stage flash plant requiring only the addition of an external heat input exchanger and pumps rated to the water flows involved.
Evaporation of the sea water takes place without the use of the conventional coils or elements and with a comparatively small heat
Layout of an MX installation: (A) booster pump, (B) starter, (C) cooling water, (D) non-return valve, (E) flow control- ler, (F) starter, (G) fresh-water pump, (H) feed indicator, (I) combined ejector, (J) probe, (K) hot water or steam in- let, (L) hot water or drain outlet, (M) salinometer alarm, (N) salinometer, and (O) drain pump.
Main components of the MX automatic sea-water distil- ler: (1) distilling condenser tube stack, (2) demister, (3) heater tube stack, 4) brine and air ejector, (5) salino- meter, (6) feed regulator, and (7) distillate pump. gradient across the transfer surfaces. This fea- ture helps to minimize scale formation. Each distiller has a shell in two parts, a heat-input tube bundle, a distilling-tube stack and two demisters located in the top half of the dis- tilling condenser. A single water-operated brine/air ejector performs the dual task of ex- tracting brine from the evaporator and air from the distiller to discharge the combined waste overboard. The quality of fresh water being distilled is monitored by a salinometer, the alarm system of which has been utilized to control the running of the fresh-water pump which supplies acceptable distillate to the ship's tanks.
The use of this alarm system to control the starting and stopping of the pump means that the traditional method of dumping unaccept- able fresh water in the bilge via solenoid-op- erated valves can be eliminated. A simple re- turn system from the suction of the fresh-water pump returns any unacceptable water to the brine section, thus eliminating spill outside the plant and maintaining a low level of brine concentration which in turn helps the quick return to normal operation.
Conclusion
In the past, when ships carried a large en- gine room crew, there was little incentive to make extensive modifications in the designs of distillers, which, if relatively costly, were reliable and familiar. Today, with much re- duced staffing and the continuing search for economy probably more progress in the over- all design of the plant has been achieved in the last five years than in the whole 70 pre- ceding years.
The dependence of ships on shore water sup- plies can now be eliminated as a matter of routine by the use of distillers which are cheap to install, easy to maintain and simple and re- liable in operation. 16 Maritime Reporter/Engineering News