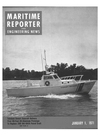
Page 28: of Maritime Reporter Magazine (January 1971)
Read this page in Pdf, Flash or Html5 edition of January 1971 Maritime Reporter Magazine
Oil Burners
In Marine Boilers
W.L. Sage and L.A. Kreidler*
The continuing trend in the marine industry toward the use of higher shaft horsepower, a greater degree of automation and increased reliabil- ity-maintainability features has led to the current high-capacity boiler designs. Parallel to the need for high- capacity boilers has been the need for high-capacity oil burners capable of obtaining complete combustion, thus offering the advantages of increased boiler efficiency, improved reliability and reduced fire-side maintenance.
The basic requirement is to provide the required supply of liquid fuel at the correct temperature, viscosity and pressure to enable the burners to atomize and inject tiny particles of oil into suitably arranged air streams, which then produce flames of the cor- rect shape and dimensions.
The concept of rapid and complete mixing of the fuel and oxident im- plies the need for a highly turbulent zone adjacent to the burner. The de- gree and type of turbulence required depend on the type and methods of fuel and air admission. If the fuel is initially well dispersed into the air stream, then small-scale turbulence is desirable. If the fuel and air are not initially well mixed, then a more mas- sive degree of turbulence is required.
The inability to obtain uniform inix- ing establishes the lower limit on ex- cess air required to obtain complete burning.
The primary function of the oil atomizer is to reduce the oil stream to small droplet size and to disperse these droplets uniformly in the com- bustion air stream. There are many approaches to accomplishing this ob- jective; however nearly all require the oil to be highly fluid (low vis- cosity).
For many years, marine boilers re- lied upon various atomizers depend- ent primarily on fuel-oil pressure as the atomization source. Capacity with these pressure atomizers was limited *Mr. Sage, research engineer, Re- search & Development Division, Al- liance, Ohio, and Mr. Kreidler, per- formance engineer, Power Generation
Division, Barberton, Ohio, Babcock &
Wilcox, presented the paper con- densed here before a recent joint meet- ing of the New York Metropolitan
Section of The Society of Naval
Architects and Marine Engineers and the New York Society of Marine Port
Engineers. due to poor atomization at low pres- sure. To obtain the needed higher capacity, dual-fluid atomizers entered the marine field. The dual-fluid atom- izers provide capacity ranges in ex- cess of 30:1 because the additional fluid has the energy required for efficient atomization in the higher ranges. Since steam usually has the lowest cost per unit of energy, it is the preferred medium.
Ignition temperature of an oil droplet is defined as the maximum temperature it can have without transposing to a higher (burning) temperature. This is not a precise temperature for a specific fuel, but is somewhat dependent on environment.
Figure 1—"Racer" sprayer plate.
Exact times for ignition and burn- ing are difficult to obtain. In a typical marine furnace where temperatures in the burner region are in excess of 3,000°F. and the atomized droplets are less than 200 microns in diameter, the predicted times are well under the times employed in marine practice.
These lead to the conclusion that under conditions normally encount- ered, the one major item controlling combustion intensity is the speed at which the air and fuel droplets can be mixed.
Hence, the problem facing the de- signer is one of promoting sufficient turbulence to obtain the desired burn- ing rates at a minimum of pressure drop. There are two commonly used methods of promoting turbulence: use of buff bodies and/or swirling flow. Both of these are also import- ant in stabilizing ignition, i.e., igni-
Principals of the joint meeting held in the Downtown Athletic Club are left to right: (seated) Joseph Thelgie, chairman of the board of directors, Society of Marine Port
Engineers; L.A. Kreidler, performance engineer, Power Generation Division, Babcock &
Wilcox Company, Barberton, Ohio; W.L. Sage, research engineer, Research & Develop- ment Division, B&W, Alliance, Ohio; Warren Signell, SNAME New York Section chair- man; (standing) Charles W. Wilson, secretary-treasurer, New York Section; Henry M.
Tiedemann, chairman, papers committee N.Y. Section; Daniel D. Strohmeier, national president of SNAME, and John Fox Jr., president, the Society of Marine Port Engineers,
New York, N.Y., Inc. tion just at or very near the burner is attained only by the recirculation of hot combustion gases.
For circular burners with pressure- type atomizers, the generally accepted approach is to use a disc stabilizer surrounding the oil gun with some degree of swirl imparted to the air.
The degree of swirl imparted has considerable influence on the flame pattern. Little or no swirl produces a cigar-shaped flame, but a high de- gree of swirl creates a more widely flared flame with a central recircu- lating core.
Streamlining the burner configur- ation prior to exiting into the furnace is beneficial in reducing pressure drop. However, a streamlined exit is not effective in promoting turbul- ence or high burning rates.
The relationship between atomizer, air register and furnace configuration is a much overlooked factor and of- ten leads to the condemnation of otherwise satisfactory components merely because they were misapplied.
Marine practice places many restric- tions on boiler design. Often the boil- ers are custom designed to fit engine- room space contours. As a result the shape of the furnace and the burner location varies from one design to another. The proper matching of the atomizer and air admission to the furnace configuration to obtain com- plete combustion, avoid flame im- pingement and minimize excess air requirements becomes more of an art than a science.
The authors' firm initiated a burn- er-development program based on marine burner requirements. The
Racer-type atomizer was selected for this test program, based on its past performance record. A cross section of the plate is shown in Figure 1.
This type of atomizer provides a means of controlling oil distribution (Continued on next page)
Figure 2—Basic burner design selected for test program with "Racer" atomizer. 30 Maritime Reporter/Engineering Hews