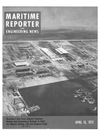
Page 4: of Maritime Reporter Magazine (April 15, 1973)
Read this page in Pdf, Flash or Html5 edition of April 15, 1973 Maritime Reporter Magazine
Shipyard Layout and Material Flow—Numbers correspond to plant facilities. Arrows show storage, (3) Plate shop, (4) Mold loft, (5) Administrative offices, (6) Electrical, plumbing material flow. Letters designate raw material receiving with A, truck shipments; B, rail, shops, (7) Pipe shop, (8) Forming slab, (9) Building ways, (10) Outfitting ways, (11) and C, barge shipments. Numbers: (1) Secondary steel storage, (2) Primary steel Launch way, (12) Outside customer storage, (1 3) Customer warehouse, and (1 4) Launch slip.
Marathon Manufacturing Company's
New Gulf Coast Shipyard
Designed By Marathon For Flexibility, The 133-Acre Brownsville, Texas Shipyard
Has The Capability Of Fabricating And Launching Drill Ships, LNG Tankers,
Work Boats, Tugs, Supply Vessels, Chemical Carriers And Other Seagoing Ships
There's a new shipyard on the
Gulf Coast and it's not like any yard in the United States or any- where else. It has been years in planning- and development but it's built and it's working.
Located on a 133-acre tract on the ship channel at the Port of
Brownsville (Texas), the new yard is the Gulf Marine Division of
Marathon Manufacturing Com- pany. Marathon (headquarters is in Houston, Texas) is a major builder of mobile offshore drilling platforms.
Marathon builds other things.
The company is a major manufac- turer of industrial metal products.
Our story, however, is concerned with one operation, shipbuilding, and one yard, Brownsville. The company has yards in Vicks'burg,
Miss, (two), in Singapore and at
Clydebank. Scotland, in addition to
Brownsville.
The Gulf Marine Division was built because Marathon could not meet a continuing heavy demand for different types of mobile off- shore drilling rigs without addi- tional facilities. Marathon designed the Brownsville plant for flexibili- ty. In addition to the offshore plat- forms, the yard has the capability of fabricating and launching drill ships, LNG tankers, work boats, tugs, supply vessels, chemical car- riers, and other seagoing ships.
Marathon's new yard combines modular construction (assembly line) techniques with conventional shipbuilding methods. Marathon feels the combination of the two concepts will permit the yard to build a number of different type vessels simultaneously—build them faster and at a lower cost.
The yard has five primary areas.
These are materials storage, the buildings which include shops and offices, the fabrication and subas- sembly area, the ways (including the building ways, outfitting and launchways) and the slip.
Steel plate comes to the yard by rail, truck and barge. Plate goes into inventory storage. The pri- mary storage area is adjacent to the Plate Shop. Capacity of this area is 20,000 tons, wit'h additional steel storage elsewhere in the yard.
The Plate 'Shop is designed for 50,000 tons of steel per year, or about 200 tons every working day.
Fabrication and material flow be- gins when a 20-ton bridge crane using a vacuum lift places the steel on a conveyor and it's moved into the shop. As it enters, the steel is descaled, shot blasted, primed and dried. At this point, the plate is transferred to one of the shop's four bays, depending on the re- quirements for the particular plate.
The Plate Shop is equipped with a bulldozer, frame benders, shears, rolls, press brakes, manipulators, turning rolls, jigs and other fix- tures. Eight overhead cranes (four at 20 tons and four at 10) serve the complete shop.
The yard's mold loft has facili- ties for full-scale drawings and produces patterns for the Plate 6 Maritime Reporter/Engineering News