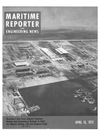
Page 5: of Maritime Reporter Magazine (April 15, 1973)
Read this page in Pdf, Flash or Html5 edition of April 15, 1973 Maritime Reporter Magazine
A semisubmersible drilling platform similar to the French-built Pentagone 81 pictured here is being built at Marathon's Brownsville, Texas yard for Societe de Forages en Mer "Neptune." The Pentagone 81 is a 5-column platform. The rig can drill in water depths to 600 feet, and its special design enables it to perform in rough sea environment.
Welder Training—Welders receive personal instruction at Marathon's new shipyard in Brownsville, Texas. Over 600 trainees have completed the course and have been certified to ABS standards. The yard has about 100 welders in the program on a con- tinuing basis. The trainees are paid for time both in the classroom and on the job.
Shop's automatic flame cutting machines. However, there are two other methods used by the yard for plate patterns. One other method is for the company draftsmen to reduce the full-scale drawings to l/10th scale. The l/10th pattern can be put under the reader on a special flame cutter and the cutting machine will convert to full scale.
Still another method is to take a picture of the l/10th scale draw- ing. A glass negative about three inches square is produced, and the negative is placed in an optic sys- tem. The drawing image is project- ed onto the steel plate and a work- er, using a tape roller, traces the pattern. The glass negative avoids the problem of distortion in pro- jection of the pattern.
Shears in the shop will handle plate to 12 feet in size and one inch in thickness. The largest of the plate rolls will take care of j^-inch steel up to a length of 36 feet. Press brakes are available to meet all re- quirements. The shop can form in- tricate shapes and angles.
Automatic welding machines are
located in the shop and in the plate
fabrication area just outside the
shop. In this assembly area, two
30- The two cranes have a clear hook
height of 65 feet.
A 150-ton-capacity dolly is used
to move components a short dis-
tance to the forming and subas-
sembly slab. The slab is about 400
feet long and about 200 feet wide
—'big enough for fabrication of
large vessel modular sections. The
slab is actually an extension of the
building ways. These ways are 200
feet wide and 1,400 feet long. Mar-
athon has installed rails the full
length of the building ways and
the slab. The rails are for a 250-
ton-capacity mobile gantry crane
which is not yet installed. The
crane will have two hooks and a
clear span of 200 feet. Hook height
will be 200 feet.
The full length of the building,
outfitting and launchways are
crossed by launch beams set on
19-foot centers. The beams have a
load bearing capacity of 16.25 tons
per linear foot.
The 250-ton gantry crane will lift
the subassembly sections from the
fabrication slab and move down
the building ways and lower the
sections onto building platens.
These sections are then joined to
form the completed vessel.
The building platens are vital to
Marathon's vessel transfer system
on the building and outfitting ways.
The platens ride the beams. With
its hydraulic transfer system, the
yard is able to move the vessels
in any of four directions. The yard
is set up for side launches. The
system permits vessel transfer
either toward or away from the
launchway, or forward or backward
parallel to the launch. This feature
offers maximum utilization of the
building/outfitting area.
On the building ways, all heavy
machinery items are placed aboard,
and major steel work is completed
while the vessel is on the building
platens and being serviced by the
250-ton gantry. After this is com-
plete, the vessel is then transported
to the outfitting ways outside the
gantry rails. At that time, another
vessel can be started on the build-
ing ways.
To this point of construction, the
vessel has gone together primarily
in a modular construction manner.
The steel fabrication processes are
either automated or semi-auto-
mated. It's on the outfitting ways
that vessel construction is more in
the conventional method of ship-
building. At this point, coating of
the vessel is accomplished. Internal
piping, electrical and machinery in-
stallation (not already in place)
may be handled during this paint-
ing process. The outfitting ways
are not served by overhead cranes.
For material handling jobs at this
point, temporary cranes are placed
aboard the vessel. These cranes are
wide - based skid - type revolving
cranes which are moved about as
need dictates.
(Continued on next page)
Components Are Huge—Shipyard workers perform tasks
on a section of a semisubmersible offshore rig. Heavy duty
material handling equipment enables the yard to fabri-
cate large components before moving to building ways.
Grinding Operation—This worker is shown as he smooths
out the steel in a tubular section of a semisubmersible
mobile offshore drilling platform. Marathon currently has
an employment of 1,800 in the new yard.
Automatic Welding Machines—These workers are using
an automatic welding machine for work on a component
section of a semisubmersible offshore drilling rig being
built at Marathon's new Brownsville shipyard.
April 15, 1973 7