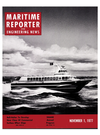
Page 46: of Maritime Reporter Magazine (November 1977)
Read this page in Pdf, Flash or Html5 edition of November 1977 Maritime Reporter Magazine
Kaiser Building Fifteen Mammoth All-Welded
Aluminum LNG Tanks For Ships At Avondale
Complexity of construction of the liquefied natural gas tanks being fabricated by
Kaiser Aluminum at its Mobile, Ala., plant can be seen in this aerial photograph.
In the background is a tank nearing completion, and the "Mobile giant" derrick which will lift the tanks into the LNG ships.
A series of huge aluminum tanks nearing completion in Mo- bile, Ala., soon will be playing a significant role in helping the na- tion meet its energy requirements.
The 15 mammoth all-welded containers are being assembled by Kaiser Aluminum & Chemical
Corporation on nearby Pinto Is- land for eventual use in three liq- uefied natural gas (LNG) ships under construction at Avondale
Shipyards in New Orleans, La.
The 125,000-cubic-meter ships will be operated by subsidiaries of El
Paso Natural Gas Company to transport natural gas at cryogenic temperatures (minus 260 degrees
F) from gas fields in Algeria to
East Coast markets.
The multimillion-dollar project is the largest of its type in LNG history, and the tanks are the first of their design ever built in this country.
The tank dimensions are im- pressive. They are being assem- bled in sets of five, and vary in size and configuration depending on where they will be placed. The largest are the three that will be in the center of the ship, with each approximately 120 feet long, 120 feet wide, and 75 feet high.
More than 27 million pounds of
Kaiser-developed 5083 aluminum plate, extrusions, and forgings are being used in the tank proj- ect. Aluminum plate up to 1% inches in thickness is provided by the company's Ravenswood,
W. Va., Works. Extrusions are from Kaiser Aluminum's Hale- thorpe, Md., plant; forgings from
Erie, Pa., Works; and the total welding wire requirements of some 500,000 pounds are being supplied by the company's New- ark, Ohio, Works.
The largest of the Conch-design rectangular containers weighs ap- proximately 950 tons, while the smaller ones weigh approximately 700 tons. They are being assem- bled at ground level and will be lifted into place in the ships by a huge twin-boom derrick which has been specially constructed for the purpose at the Mobile site.
The first tank is scheduled for lift in approximately 30 days, according to T.H. Johnson, Kaiser
Aluminum LNG project manager, and the ships are expected to be completed in 1978.
The tank fabrication itself is a two-step process. Individual com- ponent panels were assembled at a plant in Wilmington, N.C., using sophisticated processing equip- ment and automated welding tech- niques. The subassembly panels, which weighed up to 60 tons each, then were transported to Mobile by a large oceangoing barge. The barge had a capability of carrying 48 Maritime Reporter/Engineering • News
Drew Marine customers. Mr.
Smith served previously as tech- nical director, Marine Division, and will continue with this re- sponsibility for all technical sup- port to the division's sales activ- ities worldwide.
A graduate of the State Uni- versity of New York Maritime
College at Fort Schuyler, Mr.
Smith joined Drew in 1976. He served previously as manager of power generation and distribution for Allied Chemical Corporation.
Prior to that, he was employed by E.I. du Pont de Nemours, and also by Exxon Affiliates as a util- ities advisor in Holland, Singa- pore, the Philippines, Thailand, and Okinawa.
Mr. Smith is a licensed profes- sional engineer in the states of
New York, New Jersey, and South
Carolina.
Drew Chemical, a subsidiary of
United States Filter Corporation, is a major supplier of products and services for water manage- ment and specialty chemicals for the industrial and marine markets.
Drew Chemical Corp.
Promotes Walter Smith
Walter A. Smith
Raymond M. Burke, group vice president, Drew Chemical Corpo- ration, Parsippany, N.J., has an- nounced the promotion of Walter
A. Smith to director, consulting and technical services, Marine
Division. In his new position,
Mr. Smith will be responsible for establishing technical support groups in both Europe and the
Far East. This will provide more effective and efficient service to
Has The Answer To Your Corrosion Problems
CLOW PIPE PRODUCTS GROUP
P.O. BOX 516 • BENSENVILLE, IL 60106 • *
Avondale To Install
Iron Cargo Piping
Aboard U.S. Tankers
Clow Corporation, manufac- turer of cast and ductile iron pressure pipe, has announced it has received a contract from
Avondale Shipyards, New Orleans,
La., to supply 14-inch, 18-inch, and 20-inch-diameter ductile iron pipe for cargo piping in four tankers.
Although centrifugally cast ductile iron pipe has been used for ships' piping for several years by Europeans, the Avondale use, it is believed, will be its first in- stallation on a U.S.-flag vessel.
Pipe selected is standard 60,000 tensile ductile pipe which is in widespread use for underground pressure piping, except that the ductile iron will be alloyed with 2 percent nickel for added corro- sion resistance. Pipe will be plain end and joined by couplings. Duc- tile was chosen on the basis of an anticipated extended life in service, despite a higher initial cost.
The choice of ductile pipe was made following U.S. Coast Guard and American Bureau of Ship- ping approval for the use of this pipe for "cargo and ballast sys- tems."
Clow Ductile pipe and fittings, alloyed with 2% nickel, offer the most economical corrosion resistance for cargo or ballast piping. For crude, saltwater, or similar service, investigate
Clow Ductile. Clow's cargo and ballast piping meets or exceeds the require- ments of the American Bureau of
Shipping and U.S. Coast Guard.