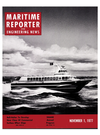
Page 47: of Maritime Reporter Magazine (November 1977)
Read this page in Pdf, Flash or Html5 edition of November 1977 Maritime Reporter Magazine
all 24 panels needed for one fin- ished tank, plus the smaller brack- ets and parts.
Upon arrival in Mobile, the panels are assembled into a tank much the same as a ship is built, with subassembly fitting and welding into place. Workmen then complete installation of all internal tank piping and instru- mentation.
Kaiser Aluminum developed special welding procedures for the project, with particular emphasis on quality control. All automatic butt welds undergo X-ray and tensile testing to insure that re- quirements are met, and string- ent inspection is followed on all manual weld operations.
When the tanks are finished, they are transported into position for eventual placement aboard ship by specially designed crawl- ers. Four of the 300-ton-capacity diesel-powered vehicles are used, one under each corner of the in- dividual tanks.
While the aluminum containers are being fabricated in Mobile,
Kaiser Aluminum also is insulat- ing the three LNG ships at Avon- dale Shipyards. The company is the prime contractor for installa- tion of a special polyurethane foam system in the holds of the carriers.
The insulation is a combination of balsa wood corners and tank support piers, nylon mesh rein- forced polyurethane foam, and fiberglass. Although not in the insulation contracting business,
Kaiser Aluminum developed the special cryogenic foam and per- fected the procedures to install it in the LNG ships. In addition to its insulating characteristics, the system has been designed as a secondary liquefied natural gas barrier, with built-in structural support for the cargo tanks.
Quality control and testing pro- cedures on the projects are con- tinuous and exceedingly strict.
At Mobile, not only is there a stringent Kaiser Aluminum in- spection program in operation, but one by the Coast Guard and by the American Bureau of Ship- ping as well. All shell welds un- dergo 100 percent X-ray inspec- tion, and each finished tank is then hydrostatically tested to in- sure integrity of the container.
Hydrostatic testing procedures for the tanks were developed by
Kaiser Aluminum, Conch, the
Coast Guard, and the ABS. Each tank is more than half filled with water, which in the case of the larger tanks is approximately four million gallons, and then eight pounds of air pressure is placed on the surface of the water.
Testing and inspecting during the foaming operations at Avon- dale Shipyards and at the Wil- mington plant are equally strict, not only by Kaiser Aluminum in- spectors but also by the Ameri- can Bureau of Shipping and the
United States Coast Guard.
MARCO Deck Machinery
Ordered For Poland
Marine Construction and De- sign Co. (MARCO), 2300 West
Commodore Way, Seattle, Wash. 98199, recently received an order from Poland's national marine agency, Centromor, for 10 sets of hydraulic machinery to be in- stalled on tuna seiners presently under construction for the USSR.
The order was formerly negoti- ated by MARCO executives dur- ing a visit to Poland earlier" this year.
Each of the 10 sets includes a
MARCO Puretic Power Block with Power Grip and a 200-hp electrohydraulic power pumping unit.
The MARCO Puretic Power
Block hauls with a pull of 7 tons and with a speed of 265 fpm.
In 1974, MARCO supplied Cen- tromor with six sets of hydrau- lic deck machinery for 53-meter (174-foot) tuna seiners which were being built in Poland for
Mexico. John R. Logan, MARCO vice president of sales, noted that the successful operation of those sets was an important factor in Centromor's decision to again use MARCO hydraulic deck ma- chinery.
PHILLYB0ND BLUE
Hull Fairing and Smoothing Compound
Two component epoxy paste with unsurpassed application characteristics, toughness and durability for structural or cosmetic purposes
PHILLYBOND BLUE was one of several Philadelphia Resins' products chosen for use on the USCG-C ice breaker, Polar Star, built by Lockheed Shipbuilding.
The smooth consistency and ex- cellent non-sagging properties of
PHILLYBOND BLUE make it unex- celled for leveling rough or pitted plating, forming fillets or smoothing weld seams. PHILLYBOND BLUE is particularly useful in preparing rough or pitted surfaces of hulls, tanks, sonar domes for top coating or lining. This easy-to-apply fairing and smoothing compound retains tenacious bond under extremes of temperature, shock and environment.
For older vessels, PHILLYBOND BLUE is unexcelled for fairing and smoothing rough or pitted rudder and hull surfaces.
Phillybond Blue excellent for emergency repairs to pump casings, sea chests, condenser boxes and numerous other com- mercial ships' applications.
DEALER INQUIRIES INVITED ^Ask for Qur new Adhesives and Laminating brochure)
Manufacturers of Chockfast®, Phillystran®, Phillybond®, Phillyclad®
PHILADELPHIA RESINS
PHILADELPHIA RESINS CORPORATION 20 Commerce Drive, Montgomeryville, Pa. 18936 Area Code 215-855-8450
Telex 84-6342 Cable: Philres MMLL
November 1, 1977 47